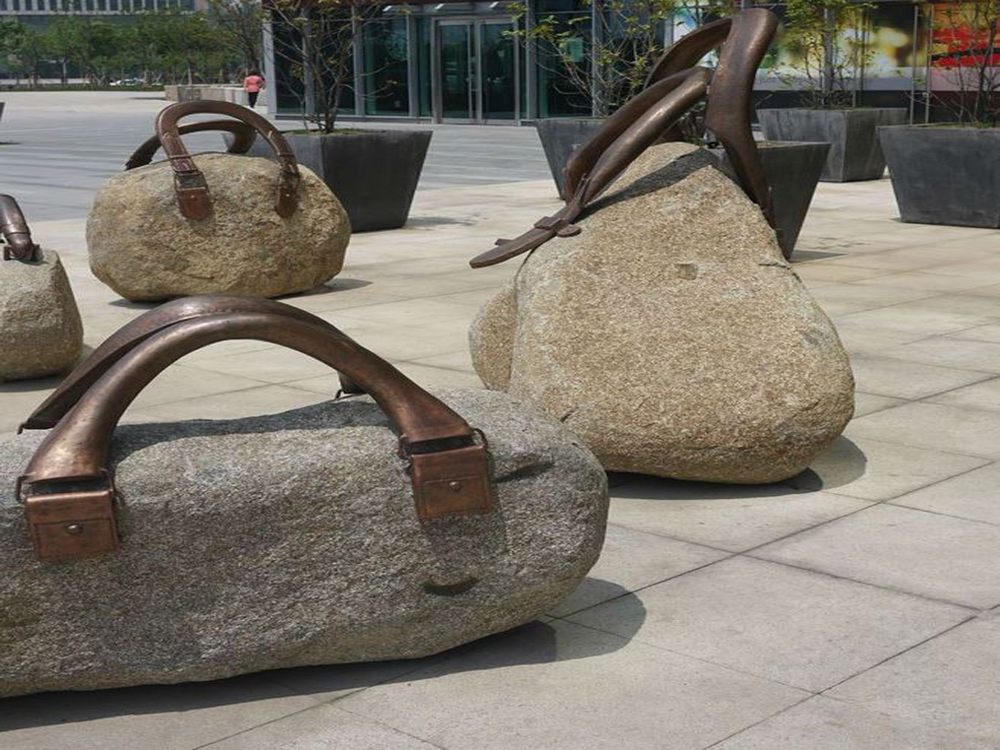
Creating a large porcelain sculpture is a meticulous and labor-intensive process that demands exceptional skill and patience. The journey begins with clay preparation, where the raw material is carefully mixed, wedged, and kneaded to remove air bubbles and achieve the right consistency. This stage is crucial, as any imperfections can lead to cracks or breaks during firing.
Next comes shaping and sculpting, often the most time-consuming phase. Artists use hand-building techniques like coiling, slab construction, or wheel-throwing to form the sculpture's basic structure. Larger pieces may require internal supports or armatures to prevent collapse. Delicate details are added layer by layer, requiring steady hands and precision.
Once shaped, the sculpture enters the drying stage, which can take weeks for large pieces. Uneven drying can cause warping, so artists often cover the work with plastic or damp cloths to control moisture loss. After drying, the piece undergoes bisque firing at a lower temperature to harden the clay without vitrifying it.
The glazing process follows, where multiple layers of glaze are applied by brushing, dipping, or spraying. This step demands expertise, as uneven application can ruin the sculpture's aesthetics. Finally, the piece undergoes high-temperature firing, where the glaze melts and fuses with the clay, transforming it into a durable, luminous artwork. Each stage requires unwavering attention, making porcelain sculpture creation a true test of craftsmanship.