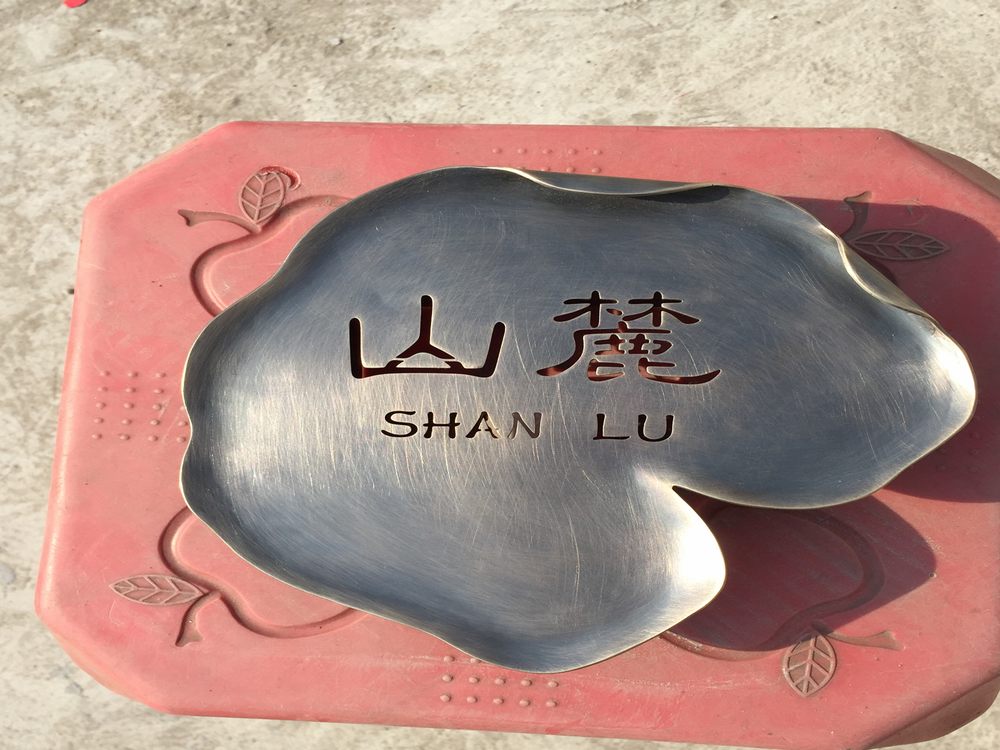
Maintaining color consistency across batches of porcelain sculptures is a complex challenge that artisans and manufacturers face. The primary difficulties stem from variations in raw materials, where subtle differences in clay composition or mineral impurities can alter fired colors unpredictably. Glaze formulation presents another hurdle, as precise chemical balances must be maintained—even minor deviations in metallic oxides or flux agents create noticeable color shifts.
Kiln conditions prove particularly problematic, with temperature fluctuations of just 10-20°C dramatically affecting color outcomes. The positioning of pieces within the kiln also matters, as heat distribution variations create "hot spots" and "cool zones" that influence glaze reactions differently. Additionally, the hand-painting process introduces human variables; brushstroke techniques, paint dilution, and layering methods vary slightly between artisans or even the same artist across sessions.
Environmental factors like humidity during drying phases and seasonal changes in studio temperatures further complicate replication. Many studios implement rigorous quality control systems, including standardized measurement tools and digital color matching, yet the organic nature of ceramic materials ensures some degree of batch-to-batch variation remains an inherent characteristic of handmade porcelain art.