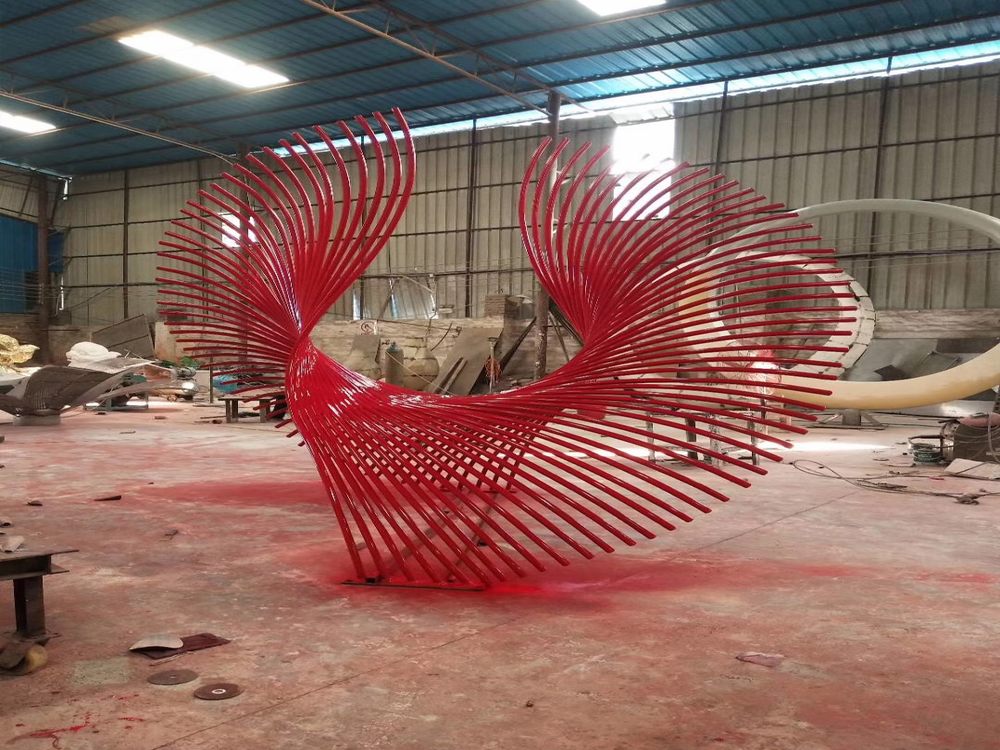
Ceramic warping during the firing process is a common challenge artists face, but skilled potters employ a variety of techniques to minimize distortion. One key method involves careful clay preparation, ensuring even moisture distribution and thorough wedging to eliminate air pockets that can cause uneven shrinkage. Artists also pay close attention to drying rates, allowing pieces to dry slowly and uniformly before firing to reduce stress fractures.
Kiln setup plays a crucial role in preventing warping. Experienced ceramicists strategically place wadding or kiln stilts under pieces to allow for even heat circulation, while adjusting shelf placement to avoid direct heat exposure. Many artists use cone packs to monitor temperature gradients within the kiln, making precise adjustments to firing schedules based on clay composition and piece thickness.
Material selection significantly impacts warping resistance. Some artists incorporate grog or sand into their clay bodies to improve structural stability, while others choose specific clay types with known thermal properties. Advanced practitioners may employ bisque firing at lower temperatures before glaze firing to strengthen the ceramic structure.
Contemporary artists are experimenting with innovative solutions like computer-controlled kilns that gradually ramp temperatures, or using refractory molds to support delicate forms during firing. Through these combined approaches of material science, technical skill, and creative problem-solving, artists successfully navigate the challenges of ceramic warping to produce stunning, stable works.