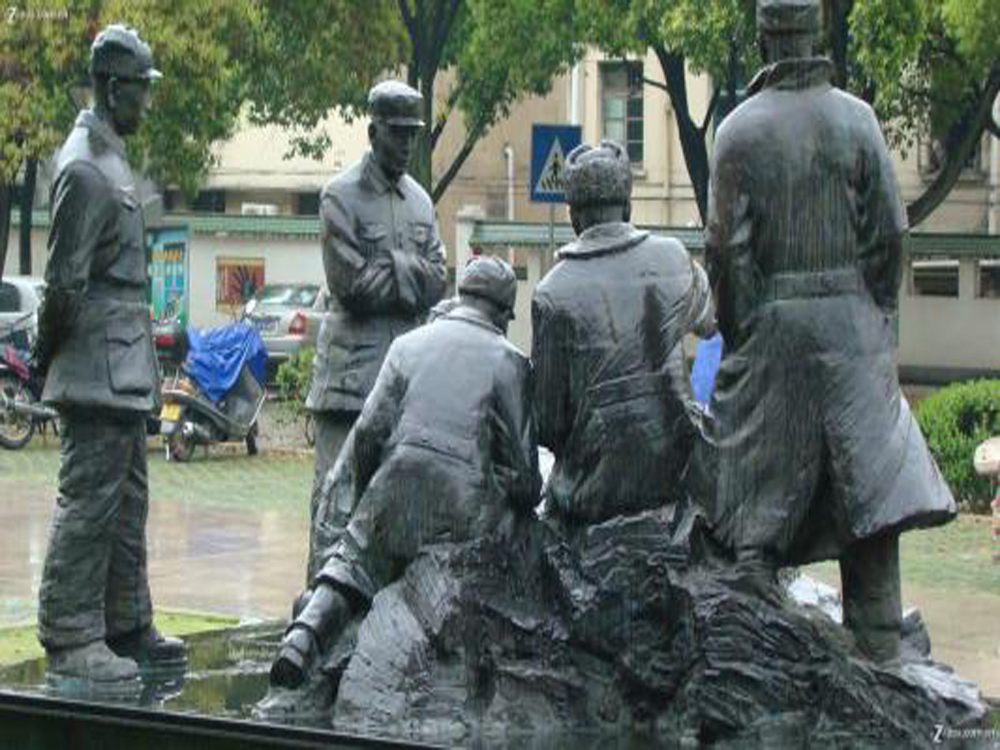
Creating porcelain sculptures with embedded luminescent materials presents unique artistic and technical challenges. One major hurdle is material compatibility—ensuring the luminescent compounds withstand high kiln temperatures without degrading or losing their glow. Artists must carefully balance the porcelain's firing requirements with the luminescent material's thermal limits, often requiring experimental glaze formulations.
Another challenge lies in achieving even light distribution. Luminescent particles can clump or settle unevenly during casting, leading to patchy illumination. Sculptors must refine their mixing and molding techniques to maintain consistency. Additionally, the translucent nature of porcelain demands precise thickness control; too thick, and the glow is muted; too thin, and structural integrity suffers.
Firing schedules also become more complex. Traditional porcelain firing cycles may damage sensitive luminescent additives, necessitating customized kiln programs with carefully controlled ramp rates and peak temperatures. Post-firing, artists face the difficulty of preserving the sculpture's delicate glow while applying protective finishes that don't obscure the luminous effects.
These challenges push ceramic artists to innovate at the intersection of ancient craft and modern material science, resulting in breathtaking works that bridge functionality and artistic expression.