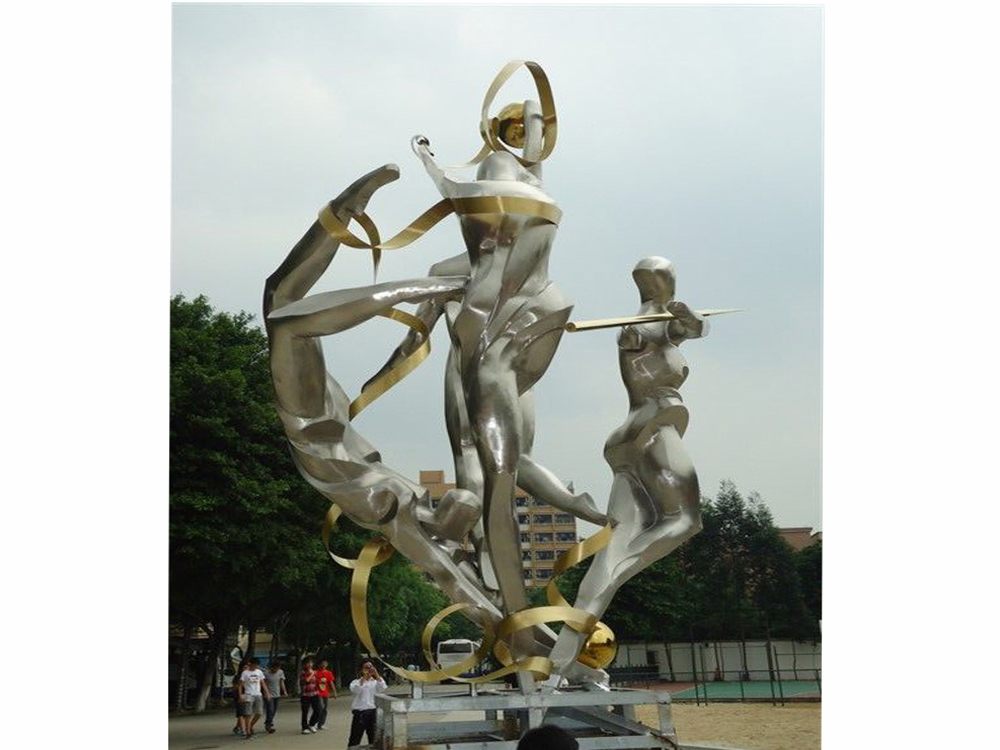
Creating porcelain sculptures with embedded pigments presents a unique set of challenges that require both artistic vision and technical expertise. Artists and manufacturers employ several innovative techniques to ensure vibrant, long-lasting results.
1. Material Selection: High-quality kaolin clay is often chosen for its purity and plasticity, while mineral-based pigments are selected for their stability under high temperatures.
2. Pigment Integration: Pigments can be mixed directly into the clay body or applied in layers. Some artists use slip-trailing techniques to embed colored clays into the base material.
3. Firing Considerations: Multiple firings at carefully controlled temperatures (often between 1200-1400°C) help preserve pigment integrity. Reduction firing can enhance certain metallic oxide pigments.
4. Surface Techniques: Many artists combine embedded pigments with surface applications like underglazes or overglazes to achieve dimensional effects.
5. Innovative Solutions: Modern manufacturers sometimes use pre-colored porcelain blends or develop custom pigment formulations to address fading or bleeding issues.
The most successful practitioners balance chemical knowledge with artistic experimentation, often developing signature techniques through years of practice. Recent advancements in nano-pigments and computer-controlled kilns are opening new possibilities for this ancient art form.