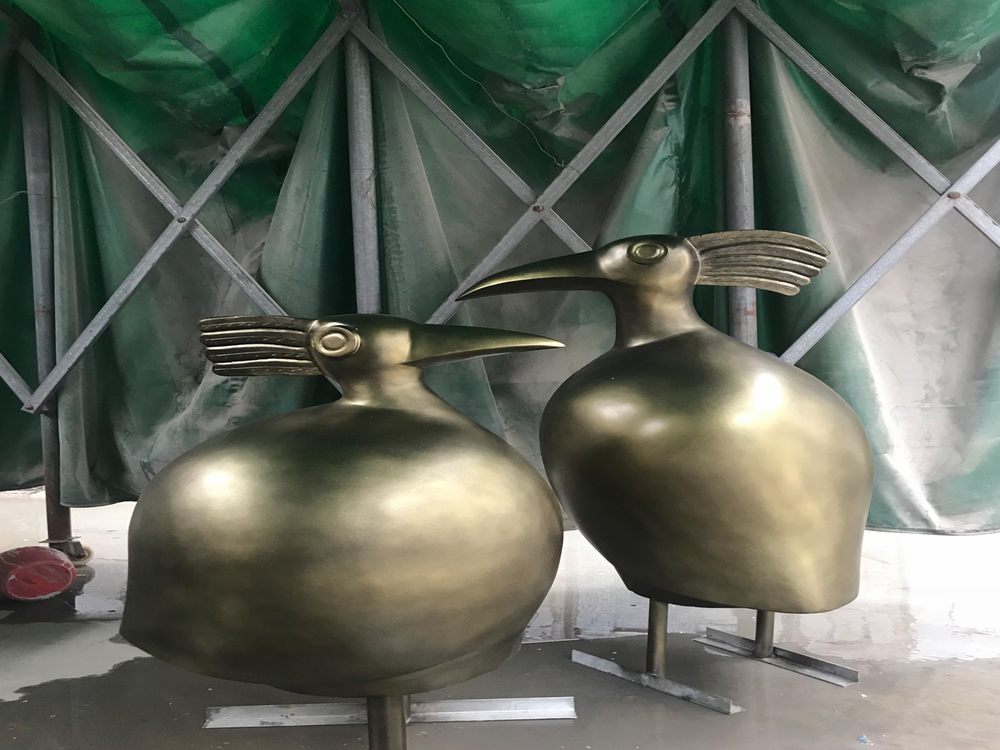
Creating porcelain sculptures with modular designs presents unique challenges for artists, requiring a delicate balance of technical skill and artistic vision. To address these hurdles, ceramic artists employ innovative methods such as precision casting, slip-casting molds, and interlocking joinery systems. Many sculptors begin by designing digital 3D models to test modular configurations before committing to clay, ensuring structural integrity while maintaining aesthetic harmony.
Experienced artisans often use specialized porcelain blends with added grog or paper fibers to improve strength during the assembly of delicate modular components. The drying process becomes particularly crucial, with controlled environments preventing warping that could compromise precise fittings. Some artists incorporate hidden reinforcement systems using porcelain "bones" or strategic internal supports that remain invisible in the finished piece.
Contemporary approaches include hybrid techniques where 3D-printed porcelain modules combine with hand-sculpted elements, allowing for both complexity and personal touch. The glazing process demands special consideration too, with artists developing custom application methods to ensure consistent coverage across separate modules while accounting for slight variations in heat absorption during firing.
Through these solutions, today's ceramic artists push the boundaries of porcelain sculpture, creating breathtaking modular works that showcase both technical mastery and creative brilliance in equal measure. The result is a new generation of porcelain art that honors tradition while embracing modern design possibilities.