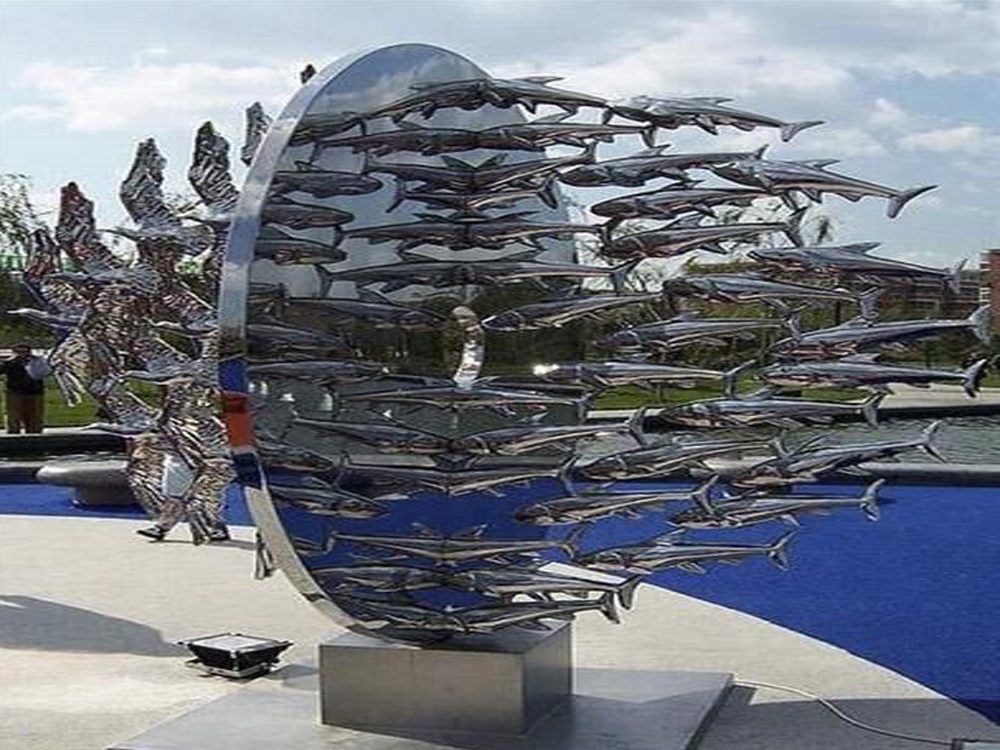
The evolution of kiln technology has dramatically transformed ceramic and industrial firing processes, with modern kilns offering significant advantages over traditional methods. In terms of energy efficiency, modern kilns utilize advanced insulation materials, precise temperature controls, and heat recovery systems, reducing energy consumption by up to 50% compared to traditional wood or coal-fired kilns. Electric and gas-powered kilns also minimize heat loss, ensuring consistent temperatures throughout the firing cycle.
Output quality is another area where modern kilns excel. Traditional kilns often produce uneven results due to fluctuating temperatures and atmospheric conditions. In contrast, modern kilns provide uniform heating, reducing defects like warping or cracking. Digital controls allow for exact replication of firing profiles, ensuring consistent quality across batches. Additionally, modern kilns can achieve higher peak temperatures, enabling the production of advanced ceramics and specialty materials that were impossible with traditional methods.
While traditional kilns hold cultural and artistic value, their inefficiency and environmental impact make them less viable for industrial-scale production. Modern kilns not only reduce operational costs but also align with sustainability goals, making them the preferred choice for contemporary manufacturing. The balance between tradition and innovation continues to shape the future of kiln technology.