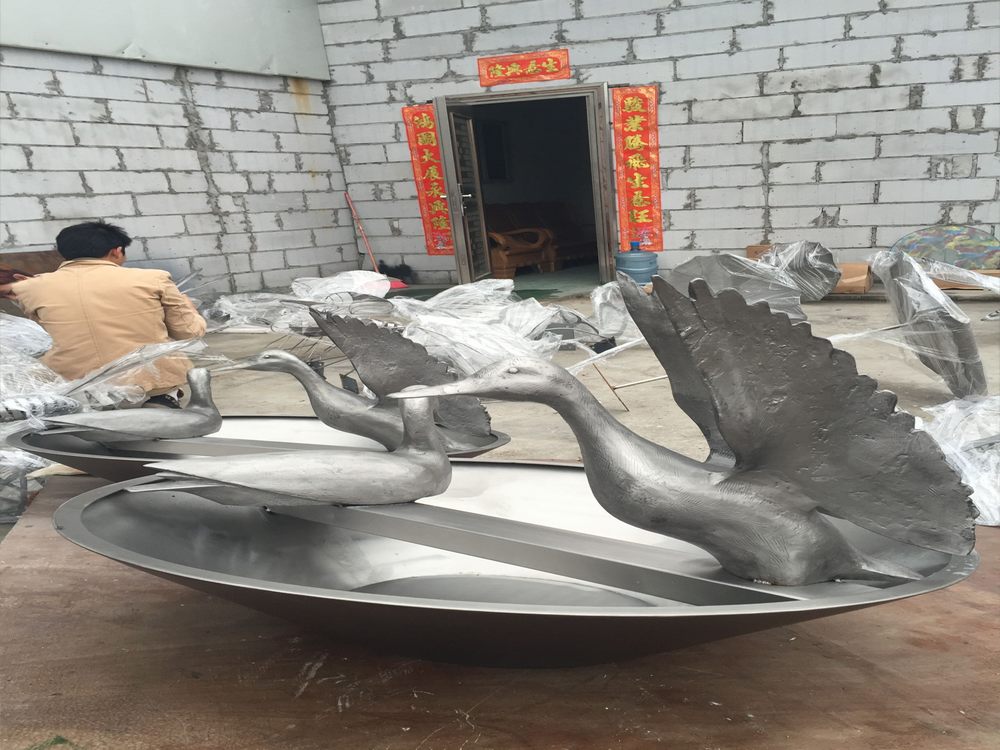
Porcelain sculptures are admired for their delicate beauty, but their production is fraught with potential defects that can compromise quality. Understanding these common issues and how to prevent them is essential for artists and manufacturers.
1. Cracks and Fissures
Cracks often occur due to uneven drying or rapid temperature changes during firing. To prevent this, ensure slow, even drying before bisque firing and control kiln temperature gradients carefully.
2. Glaze Defects (Pinholes, Crawling)
Improper glaze application or contamination can cause pinholes or crawling (glaze pulling away). Sieve glazes thoroughly, apply consistent layers, and maintain clean workspaces.
3. Warping
Thin or uneven sections may warp during firing. Reinforce delicate areas with internal supports and design sculptures with balanced thickness.
4. Bloating
Trapped air or overfiring can cause bloated surfaces. Use well-ventilated kilns and precise firing schedules, and avoid over-compacting clay.
5. Color Inconsistencies
Uneven pigment distribution or incorrect firing can lead to blotchy colors. Mix stains thoroughly and test fire small samples to verify results.
Prevention starts with quality materials and meticulous processes. Always:
- Wedge clay thoroughly to remove air pockets
- Monitor kiln conditions with digital controllers
- Conduct test firings for new designs or materials
By addressing these challenges proactively, artists can produce durable, visually stunning porcelain artworks that stand the test of time.