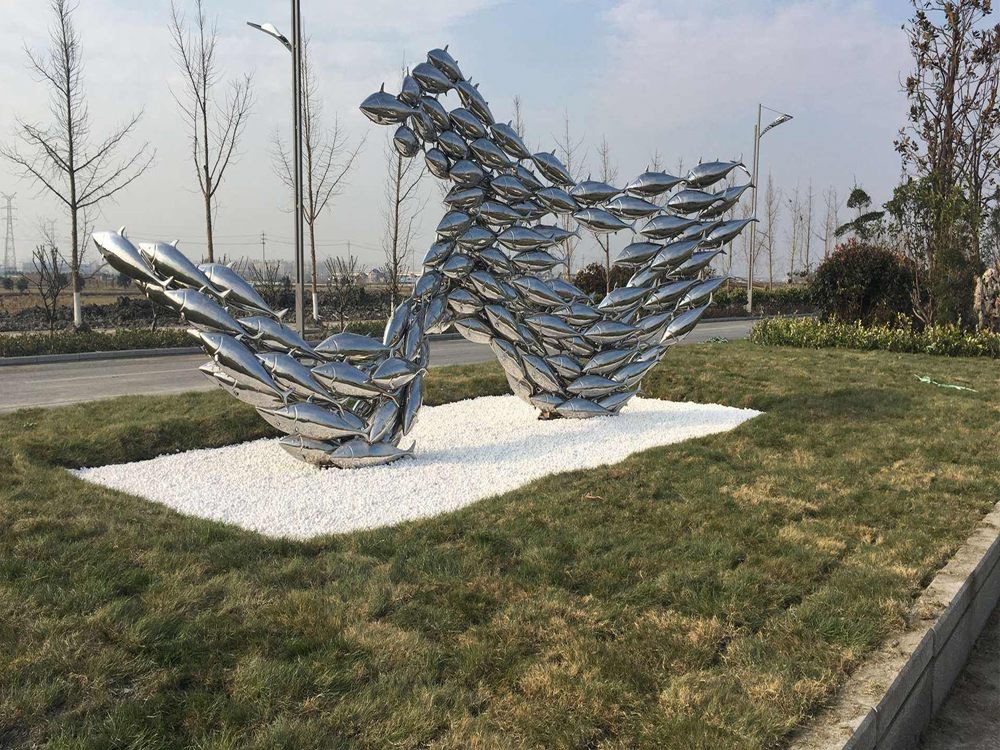
Porcelain sculpture production is a delicate art form that requires precision at every stage. However, certain phases are particularly prone to failure, often leading to costly defects or complete loss of the piece.
1. Clay Preparation and Wedging: Inconsistent clay texture or air pockets can cause cracks or warping during drying or firing. Proper wedging is essential to eliminate trapped air and ensure uniformity.
2. Shaping and Sculpting: Overworking the clay or uneven thickness can lead to structural weaknesses. Thin sections may collapse, while thick areas might not dry evenly, resulting in cracks.
3. Drying Process: Rapid or uneven drying is a leading cause of failure. If moisture evaporates too quickly, stress fractures form. Controlled drying in a humidity-controlled environment is crucial.
4. Bisque Firing: Sudden temperature changes or improper kiln loading can cause thermal shock, leading to cracks or explosions. A slow, gradual temperature increase is vital.
5. Glazing and Final Firing: Glaze application errors—such as uneven coats or incompatible glaze-clay combinations—can cause blistering, crawling, or discoloration. Overfiring may also deform the sculpture.
Understanding these critical stages helps artists and manufacturers mitigate risks, ensuring higher success rates in porcelain sculpture production. Attention to detail and controlled processes are key to mastering this timeless craft.