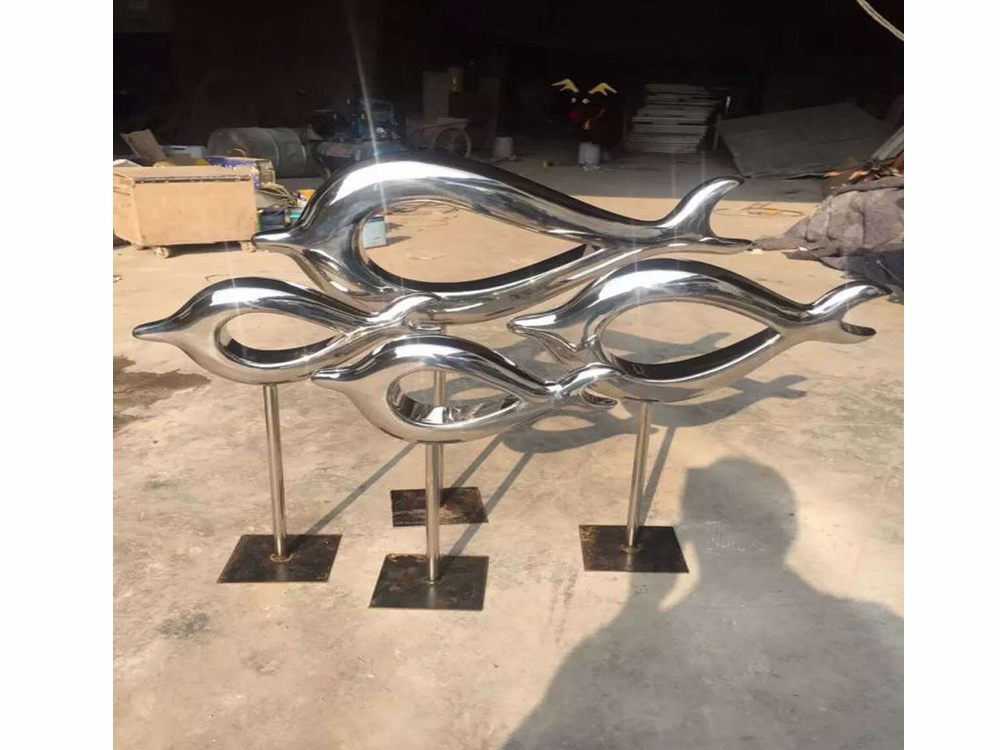
Porcelain sculptures that respond to touch or interaction represent a fascinating fusion of traditional craftsmanship and modern technology. Artists achieve this delicate balance through innovative techniques that transform fragile ceramics into dynamic works of art.
The creation process begins with specially formulated porcelain clay, often mixed with conductive materials or flexible additives. Master ceramicists shape these hybrid materials using both conventional wheel-throwing methods and advanced 3D printing technologies. The key innovation lies in embedding responsive elements within the clay body before firing - including pressure sensors, capacitive touch circuits, or shape-memory alloys that react to temperature changes.
After the initial bisque firing at lower temperatures, artists carefully install microelectronics and kinetic mechanisms in protected cavities. Some create segmented designs with hidden hinges, while others incorporate piezoelectric elements that generate subtle vibrations when touched. The final high-temperature firing requires precise control, as components must survive the kiln's extreme heat without compromising the porcelain's translucency.
Contemporary artists like Ying Gao and Zimoun have pioneered techniques using conductive glazes that complete circuits when touched, triggering light or sound responses. Others employ ferrofluid-filled porcelain vessels that reshape when exposed to magnetic fields from viewers' movements. These interactive pieces challenge porcelain's traditional static nature while maintaining its exquisite aesthetic qualities.
The result transforms passive observation into active participation, inviting viewers to complete the artwork through their touch. This emerging art form continues to evolve as ceramicists experiment with smart materials, proving that even ancient mediums can find new life in interactive experiences.