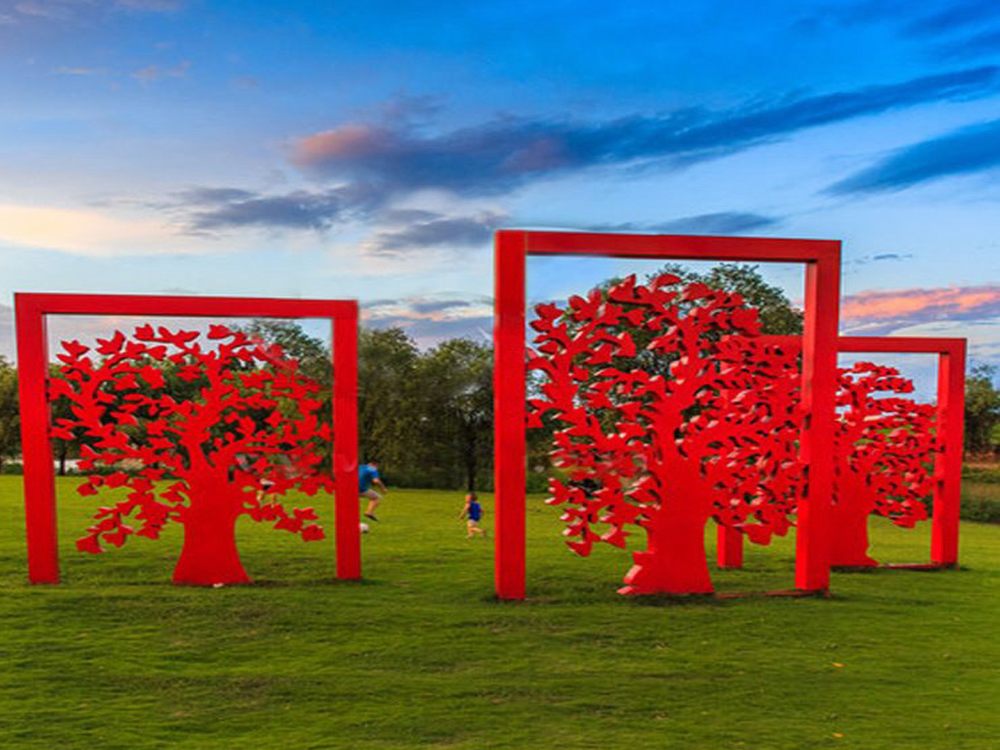
Creating porcelain sculptures with integrated lighting or electronic elements is a fascinating fusion of traditional ceramic art and modern technology. Artists begin by designing the sculpture with hollow cavities or thin-walled sections to accommodate wiring and light sources. The porcelain clay is carefully shaped, often using slip-casting or hand-building techniques, ensuring precise thickness to allow light diffusion while maintaining structural integrity.
Before firing, channels for wiring are carved or molded into the design. Some artists embed LED strips or fiber optics during the sculpting process, while others install lighting after the final kiln firing. For electronic components, waterproofing and heat-resistant materials are crucial considerations. The translucent quality of porcelain makes it ideal for lighting effects, as it softly diffuses light without losing its ceramic elegance.
Advanced techniques include using conductive porcelain paints to create circuit patterns directly on the sculpture's surface, or incorporating wireless charging to power embedded LEDs. The final pieces often require collaboration between ceramic artists and electrical engineers to ensure both artistic vision and technical functionality are achieved. This innovative approach transforms traditional porcelain into dynamic, illuminated artworks that bridge craft and technology.