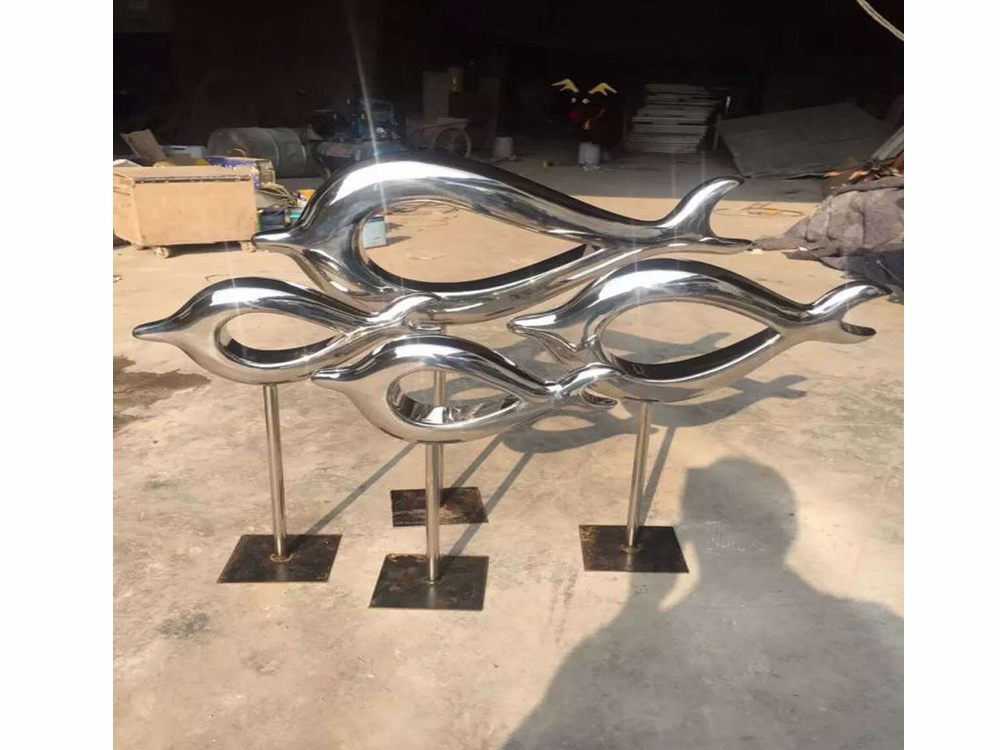
Creating large porcelain sculptures is a delicate art that requires meticulous attention to prevent warping and cracking during drying and firing. Here are key techniques used by master ceramicists:
1. Slow and Even Drying: To avoid uneven shrinkage, sculptures are dried gradually in a controlled environment. Covering the piece with plastic or using damp cloths helps regulate moisture loss.
2. Reinforcement with Armatures: Internal supports like wire or clay coils provide structural stability, reducing stress during drying.
3. Proper Clay Preparation: Wedging clay thoroughly removes air pockets, while grog (fired clay particles) mixed into the clay body minimizes shrinkage and cracking.
4. Controlled Firing Cycles: A slow bisque firing (pre-firing) at low temperatures ensures moisture evaporates completely before the final high-temperature firing.
5. Use of Kiln Furniture: Shelves and stilts in the kiln promote even heat distribution, preventing thermal shock.
6. Post-Firing Cooling: Allowing the kiln to cool naturally prevents sudden temperature changes that could cause cracks.
By mastering these techniques, artists can create stunning, durable porcelain sculptures free from defects.