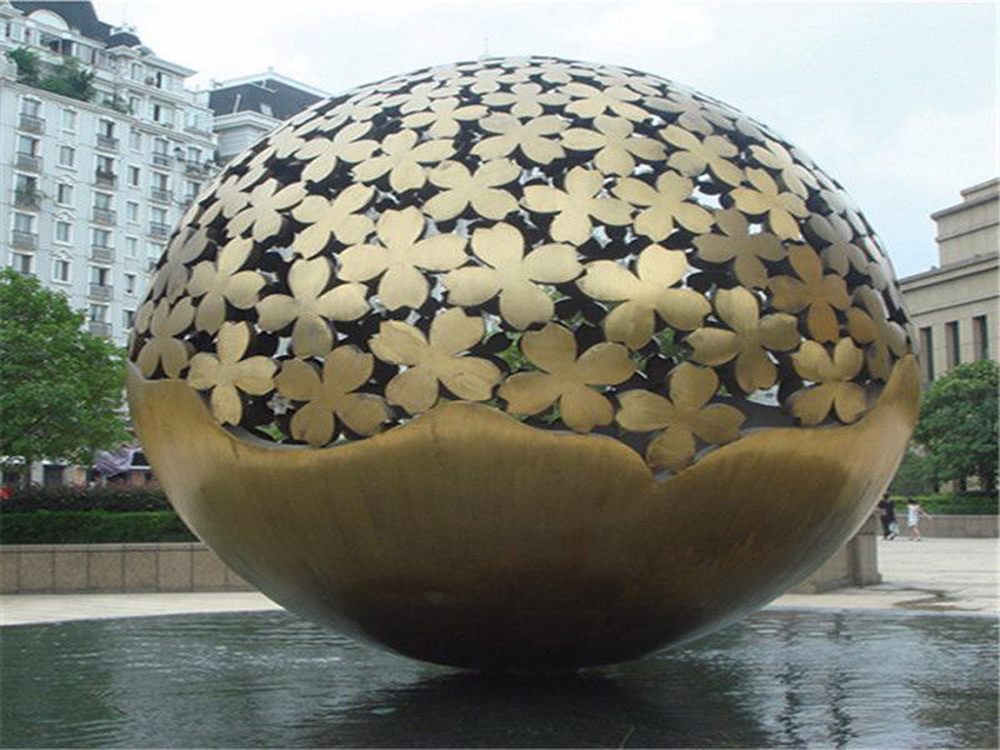
Museums employ sophisticated methods to protect delicate porcelain sculptures while making them accessible to the public. The preservation process begins with strict environmental controls - maintaining stable temperature (20-22°C) and relative humidity (45-55%) to prevent cracking and glaze deterioration. Specialized LED lighting with UV filters minimizes light exposure to 50 lux or less, significantly reducing photochemical damage.
For display, conservators use custom-designed mounts that support sculptures without stress points, often made from inert materials like acrylic or padded stainless steel. Many institutions rotate fragile pieces every 3-6 months to limit exposure. Advanced cases feature microclimate systems with oxygen scavengers and silica gel to create protective atmospheres.
Handling follows strict protocols: cotton gloves prevent oil transfer, and sculptures are always supported from their sturdiest sections. Some museums apply thin protective coatings of Paraloid B-72, a reversible acrylic resin. Digital preservation through 3D scanning creates backup records while allowing virtual access to reduce physical handling.
Recent innovations include vibration-dampening platforms and real-time condition monitoring with wireless sensors that track temperature, humidity, and structural integrity. These comprehensive approaches allow museums to balance public access with long-term preservation of these culturally significant artworks.