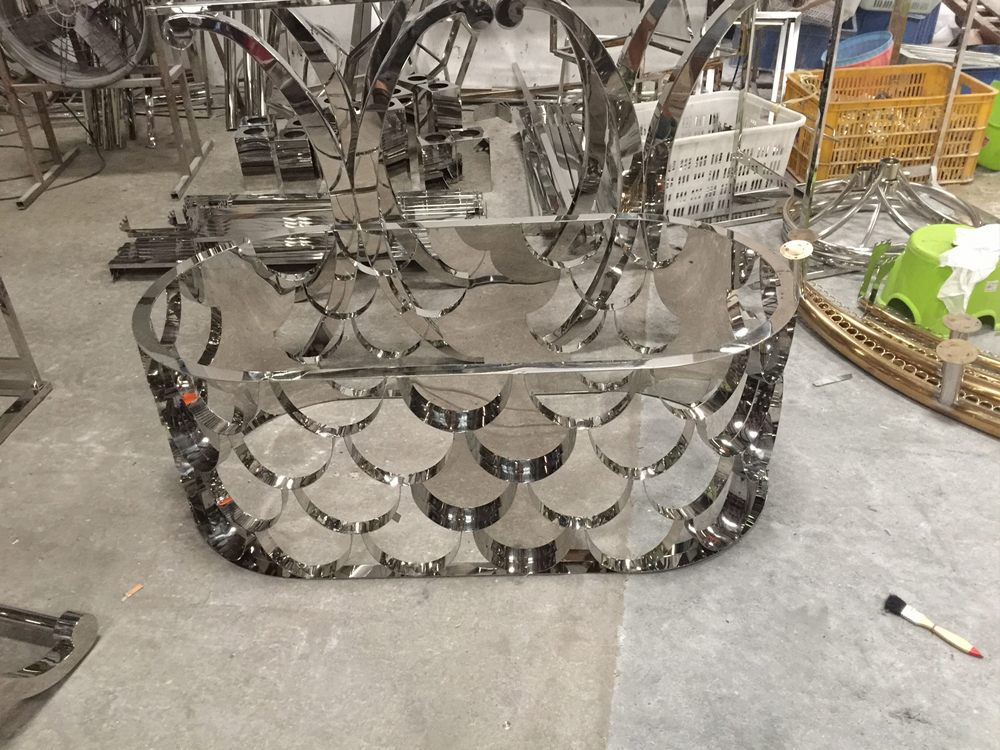
Creating flawless seams in slip-cast porcelain sculptures is a delicate art that demands precision and expertise. One of the most common challenges is mold misalignment, where even a slight shift between mold halves can leave visible seams. Artists often struggle with air bubbles trapped at the joint lines, which weaken the structure and create imperfections.
Clay shrinkage during drying and firing presents another hurdle, as uneven contraction can distort seams. The viscosity of the slip also plays a crucial role - too thin and it won't fill mold details properly, too thick and it creates uneven edges. Many sculptors find removing mold lines particularly difficult without damaging the fragile greenware.
Advanced techniques like using fine-grit sandpaper or diamond files help refine seams, while proper mold design with registration keys minimizes alignment issues. Some artists employ specialized tools like seam rollers or apply slip trailing to reinforce weak joints. Understanding these challenges is key to producing museum-quality porcelain pieces with invisible seams.