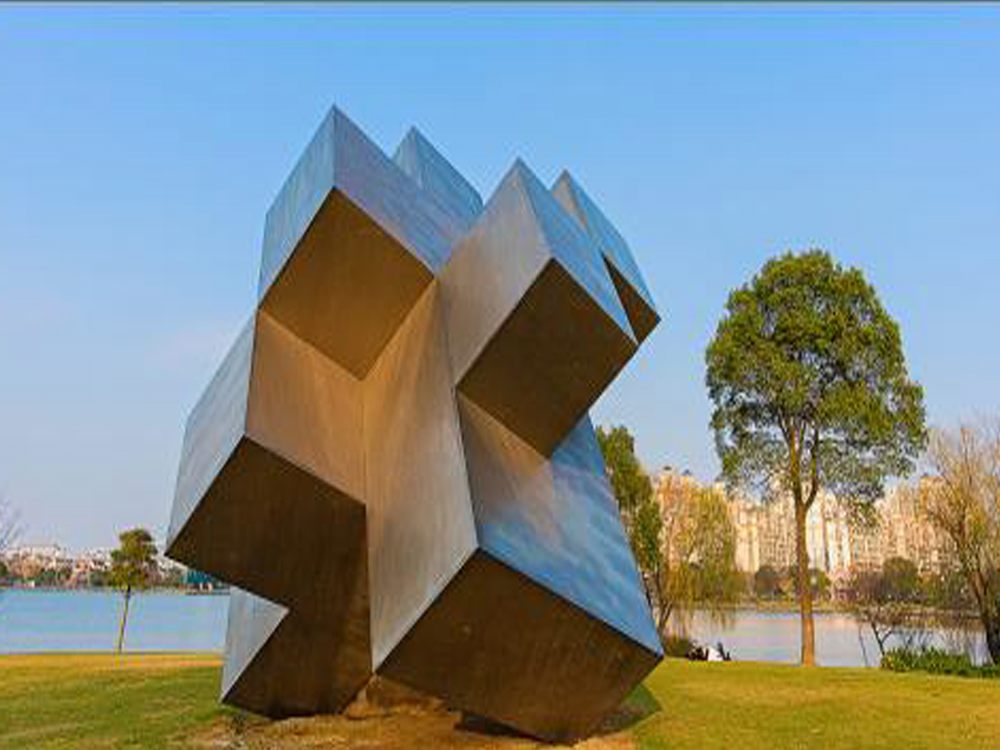
Creating hand-built porcelain sculptures is a delicate art form that demands precision, patience, and skill. One of the most critical yet challenging aspects of this craft is achieving a flawless join between different pieces of porcelain. Whether assembling limbs on a figurine or attaching intricate details, imperfections in joining can compromise the structural integrity and aesthetic appeal of the final piece.
The primary challenge lies in the nature of porcelain itself. Its low plasticity makes it prone to cracking or warping during drying and firing. When joining wet or leather-hard clay, uneven shrinkage rates between sections can lead to weak bonds or visible seams. Additionally, air bubbles trapped in the slip or scoring marks may cause gaps or fractures after firing.
Timing is another crucial factor. Joining pieces at slightly different moisture levels often results in stress points that manifest as cracks later. Even experienced artists struggle with maintaining consistent thickness across joints, as thin areas dry faster and create tension.
Firing presents its own set of difficulties. The high temperatures required for porcelain (typically 1200-1400°C) can exaggerate any minor imperfections in joins. Differential thermal expansion between joined sections might cause separation or cracking during the kiln process.
To overcome these challenges, artists employ various techniques: precise scoring and slipping methods, using paper clay for repairs, controlling drying environments, and sometimes incorporating hidden supports. Mastering these approaches requires both technical knowledge and artistic sensitivity, making flawless joining one of the true tests of a porcelain sculptor's expertise.