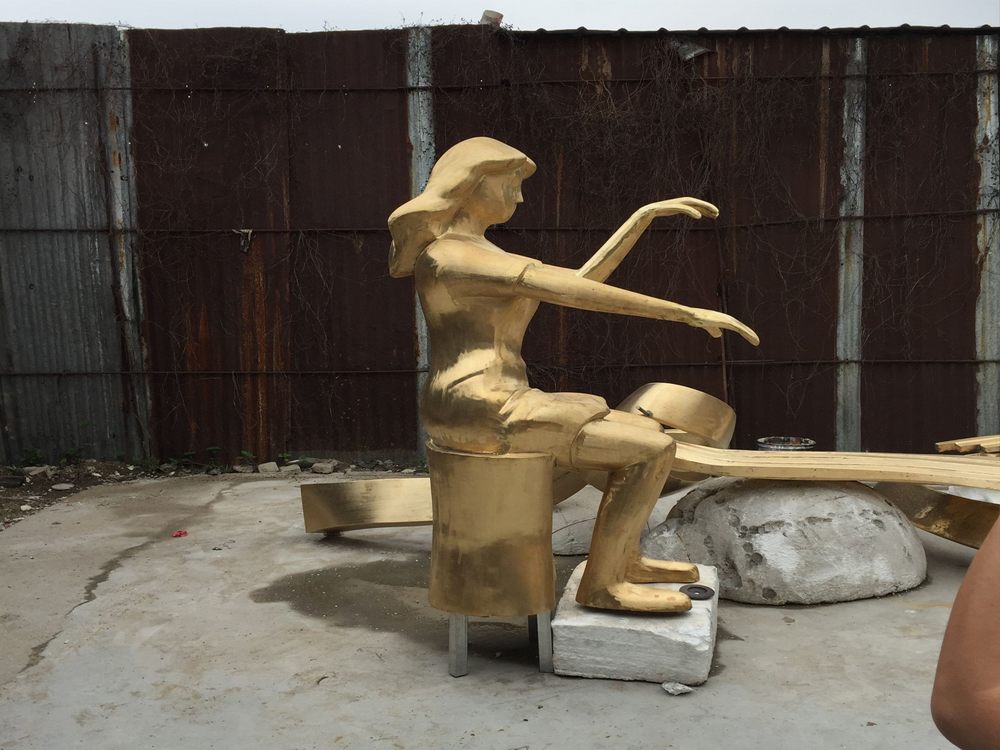
Creating stunning crystalline glazes on porcelain sculptures requires meticulous attention to the firing schedule. The ideal schedule depends on several critical factors, including kiln temperature, ramp rates, hold times, and glaze composition.
1. Kiln Temperature: Crystalline glazes thrive at specific temperatures, typically between 1200°C and 1300°C. Precise control ensures proper crystal formation without over-firing.
2. Ramp Rates: Slow heating (50-100°C per hour) allows glaze components to melt evenly, while rapid cooling can disrupt crystal growth. A gradual cooling phase is essential for well-defined crystals.
3. Hold Times: Extended soaking periods at peak temperature encourage larger crystal development. Shorter holds yield finer, more delicate patterns.
4. Glaze Composition: High zinc or silica content promotes crystallization, while additives like titanium or iron oxide influence color and texture.
5. Kiln Atmosphere: Oxidation or reduction firing affects glaze behavior. Oxidation is preferred for brighter crystals, while reduction may deepen colors but complicate crystallization.
By balancing these factors, artists can achieve breathtaking crystalline effects on porcelain sculptures, transforming them into unique works of art. Experimentation and precise record-keeping are key to mastering this intricate process.