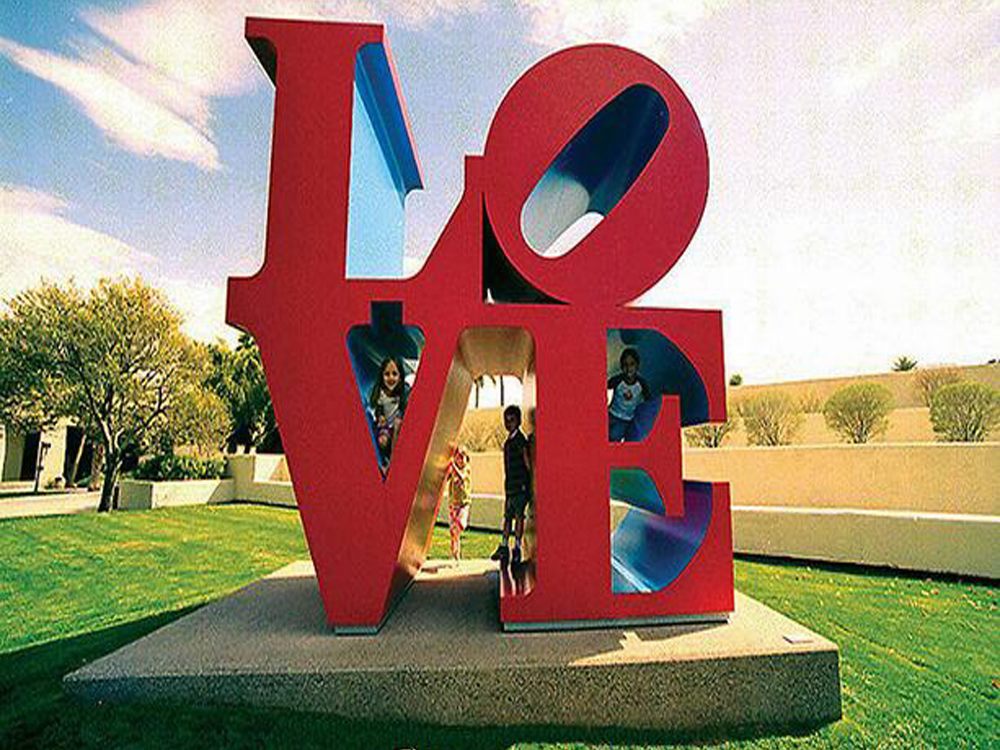
Creating porcelain sculptures with high-gloss finishes is a delicate art form that requires precision, patience, and expertise. One of the most common challenges is achieving an even glaze application. Porcelain’s smooth surface can cause the glaze to pool or drip unevenly, leading to imperfections. Artists must master the right consistency and application techniques to ensure a flawless finish.
Another significant hurdle is the firing process. High-gloss finishes demand precise kiln temperatures; even minor deviations can result in cracks, bubbles, or dull spots. Controlling the kiln environment, including heating and cooling rates, is critical to preserving the sculpture’s integrity and shine.
Additionally, the fragility of porcelain poses a challenge. The material is prone to warping or breaking during handling, especially before the final firing. Sculptors must balance structural stability with aesthetic detail, often reinforcing delicate areas without compromising the design.
Lastly, color consistency can be tricky. High-gloss glazes may shift in hue during firing, requiring artists to test and adjust formulas repeatedly. Achieving the desired vibrancy and transparency adds another layer of complexity to the process.
Despite these challenges, mastering high-gloss porcelain sculptures is immensely rewarding. With practice and attention to detail, artists can create stunning, luminous works that captivate viewers.