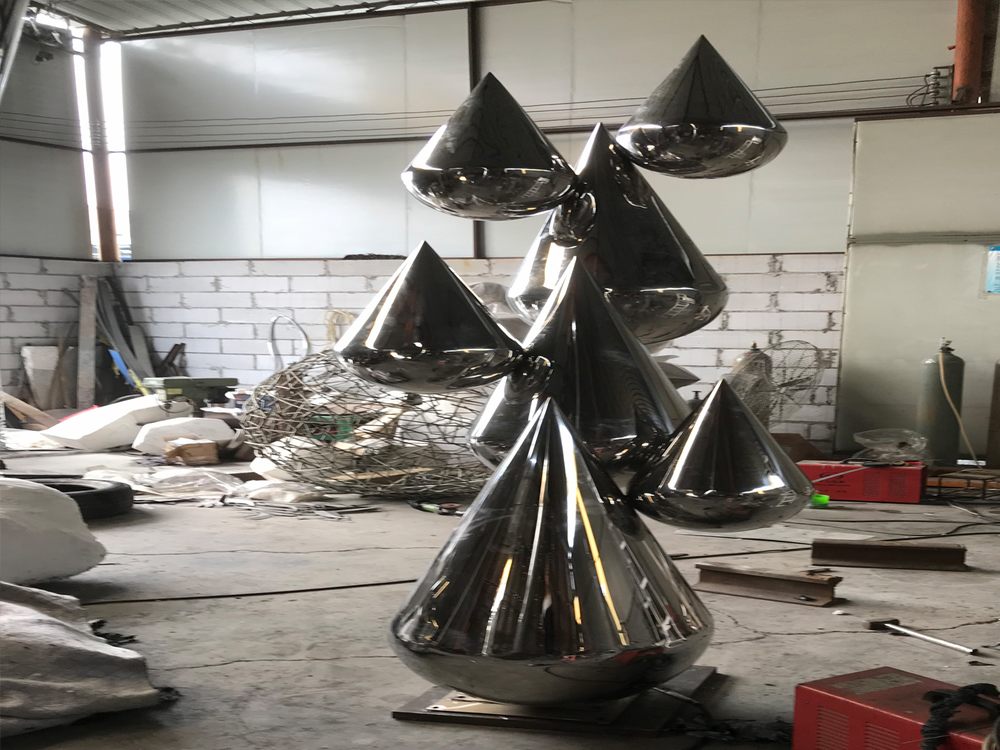
Creating flawless porcelain sculptures requires meticulous attention to the drying and firing stages, where cracks and warping often occur. Artisans employ several expert techniques to ensure structural integrity.
1. Controlled Drying Process
- Slow, even drying prevents rapid moisture loss, which causes cracks.
- Sculptures are wrapped in plastic or placed in humidity-controlled chambers.
- Thicker sections are dried gradually to avoid uneven shrinkage.
2. Proper Clay Preparation
- High-quality, well-wedged clay minimizes air bubbles that lead to fractures.
- Adding grog (pre-fired clay particles) improves durability and reduces warping.
3. Strategic Kiln Firing
- A slow bisque firing (under 1000°C) removes residual moisture safely.
- Glaze firing is done in stages to prevent thermal shock.
- Kiln shelves are leveled to ensure even heat distribution.
4. Support Structures
- Temporary clay props or stilts support delicate sections during firing.
- Hollow sculptures are vented to allow steam to escape.
5. Post-Firing Adjustments
- Cooling happens gradually inside the kiln to prevent sudden contraction.
- Minor warping can be corrected with careful grinding or refiring.
By mastering these methods, artisans achieve crack-free, perfectly shaped porcelain masterpieces. Patience and precision are key to preserving the sculpture’s beauty from clay to kiln.