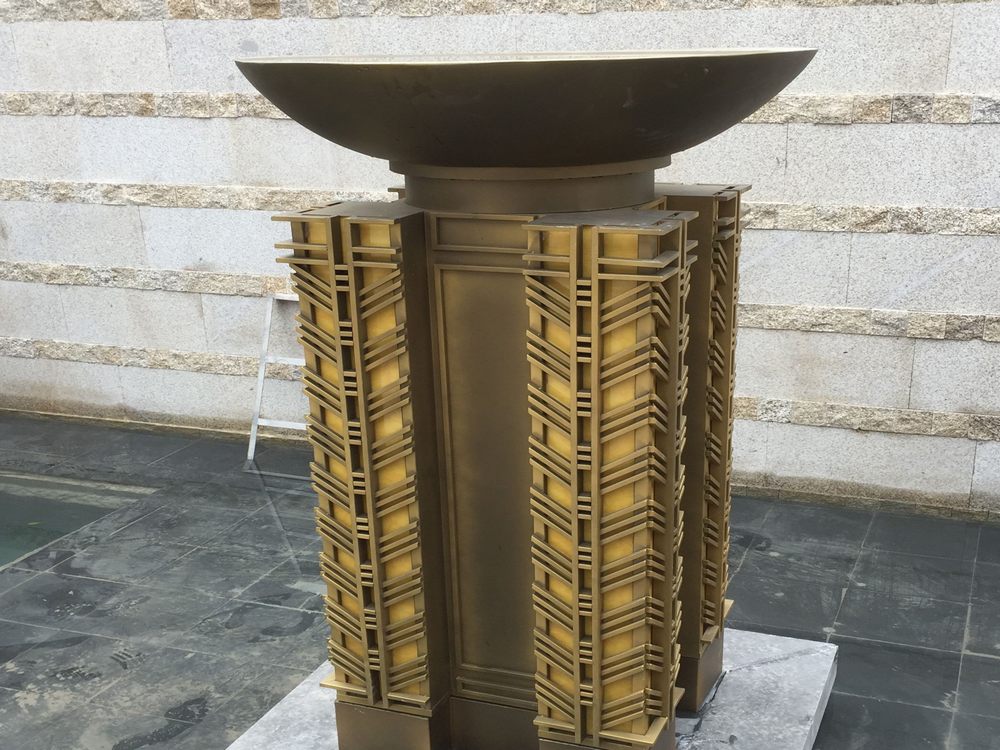
Porcelain sculptures, especially antique pieces, hold significant cultural and monetary value. When damage occurs, restoration experts employ meticulous techniques to repair chips, cracks, or breaks while preserving the artwork's integrity.
The process begins with a thorough assessment to determine the extent of damage and original materials used. Experts then clean the damaged area carefully, removing dirt or old adhesives that might interfere with repairs. For chips, they use reversible epoxy resins or ceramic powders mixed with binding agents to fill gaps seamlessly.
Color matching is critical—restorers analyze the original glaze and pigments to recreate an identical hue. They often apply thin layers of paint, firing each layer in low-temperature kilns to achieve authenticity. For structural breaks, specialists use adhesives that maintain flexibility to prevent future stress cracks.
Crucially, all materials used are reversible, ensuring future conservators can undo repairs if better techniques emerge. Documentation accompanies each restoration, detailing every step taken—a practice that maintains provenance and value.
Advanced tools like UV lights help detect hidden fractures, while microscopes assist in precision work. The goal is always "invisible repair"—where damage becomes undetectable to the untrained eye but remains identifiable under professional scrutiny, adhering to museum conservation ethics.
By combining traditional craftsmanship with modern technology, restoration experts breathe new life into porcelain masterpieces while safeguarding their historical and financial worth for generations to come.