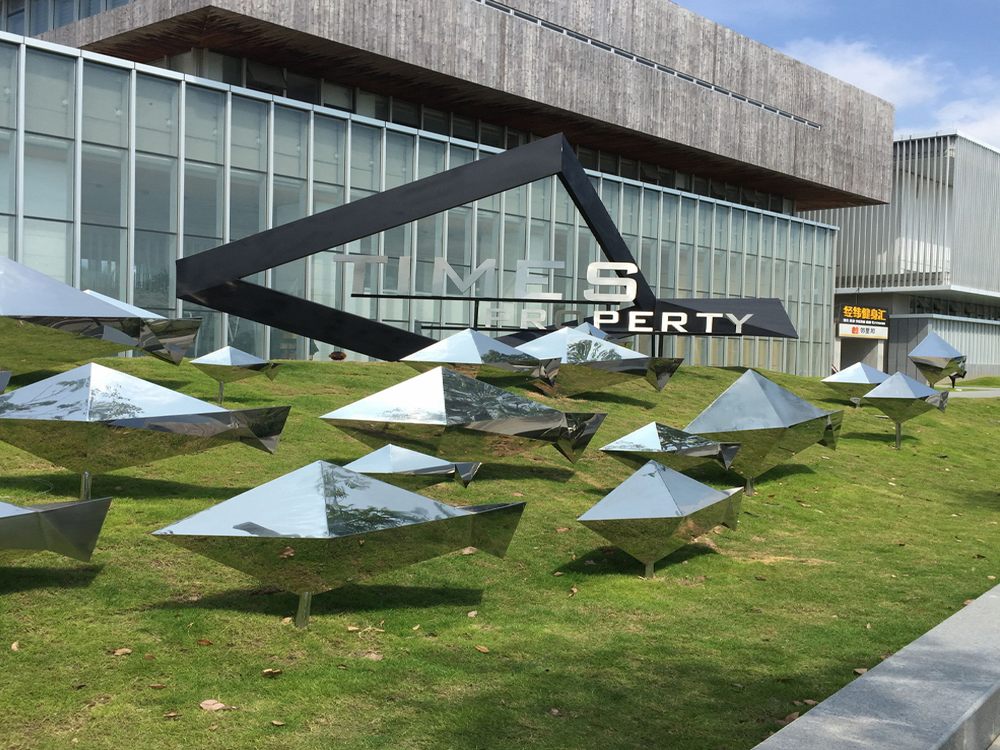
Creating large porcelain sculptures is a delicate dance between artistic vision and engineering precision. Artists achieve this balance through meticulous material selection, innovative design techniques, and specialized firing processes.
The foundation begins with high-quality porcelain clay, chosen for both its plasticity and fired strength. Experienced ceramicists often blend different clay bodies or add strengthening materials like grog to enhance structural stability without compromising workability.
Design considerations play a crucial role. Artists employ hollow construction methods, creating internal support systems that distribute weight evenly. Strategic thickening at stress points and gradual tapering of forms help prevent cracking during drying and firing.
The firing process itself becomes an art form. Large pieces require carefully controlled kiln environments with extended heating and cooling cycles to prevent thermal shock. Some artists use multiple lower-temperature firings to gradually strengthen the piece before the final high-temperature vitrification.
Surface decoration integrates with structural needs. Glazes are formulated not just for visual effect but also to complement the clay body's expansion properties. Texturing techniques may serve dual purposes - creating visual interest while strategically reinforcing vulnerable areas.
Contemporary artists often combine traditional ceramic wisdom with modern technology. Digital modeling helps predict stress points, while innovative kiln designs accommodate oversized works. The result is breathtaking sculptures that stand the test of time, both as artistic statements and physical objects.
This careful equilibrium between form and function elevates porcelain sculpture beyond mere decoration, transforming fragile clay into enduring monuments of human creativity.