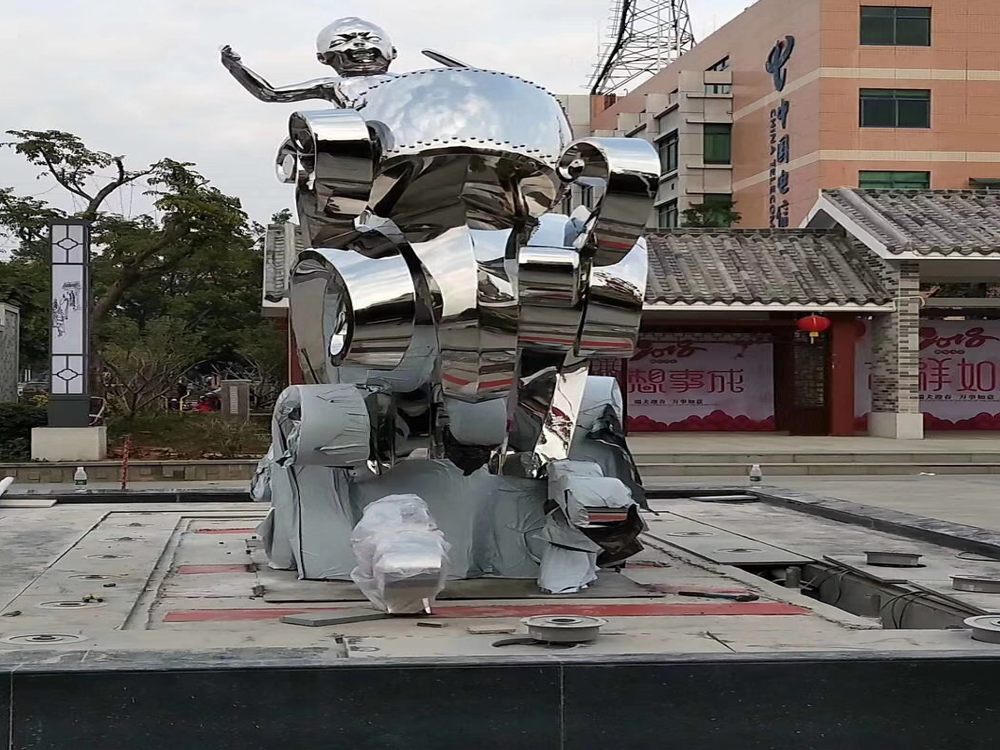
Porcelain, renowned for its delicate beauty and surprising strength, presents a unique challenge for artists. Achieving the perfect equilibrium between fragility and durability requires a deep understanding of materials and meticulous craftsmanship.
The journey begins with clay selection. Artists often blend kaolin with other minerals to enhance plasticity while maintaining structural integrity. Wedging the clay thoroughly removes air bubbles that could cause weakness, while proper drying prevents cracks before firing.
Kiln mastery forms the cornerstone of durable porcelain. A carefully controlled bisque firing at lower temperatures (900-1000°C) prepares the piece for glazing. The final high-temperature firing (1200-1400°C) triggers vitrification, where clay particles fuse into a glass-like matrix that grants porcelain its characteristic strength.
Glazing techniques contribute significantly to durability. Multiple thin layers create a protective shell without compromising delicate details. Some artists employ crystalline glazes that form reinforcing microstructures during cooling. Others use underglaze decorations protected by transparent overglazes.
Structural design plays a crucial role. Experienced potters reinforce thin areas with subtle curves or supporting elements hidden in the design. The thickness-to-height ratio is carefully calculated to prevent collapse while maintaining elegant proportions.
Modern innovations include nano-particle infusions that strengthen porcelain without altering its appearance. Some contemporary artists even incorporate fiber reinforcements invisible to the naked eye.
Through this alchemy of science and artistry, porcelain masters create works that appear impossibly delicate yet withstand centuries, proving that true craftsmanship lies in balancing opposing qualities to perfection.