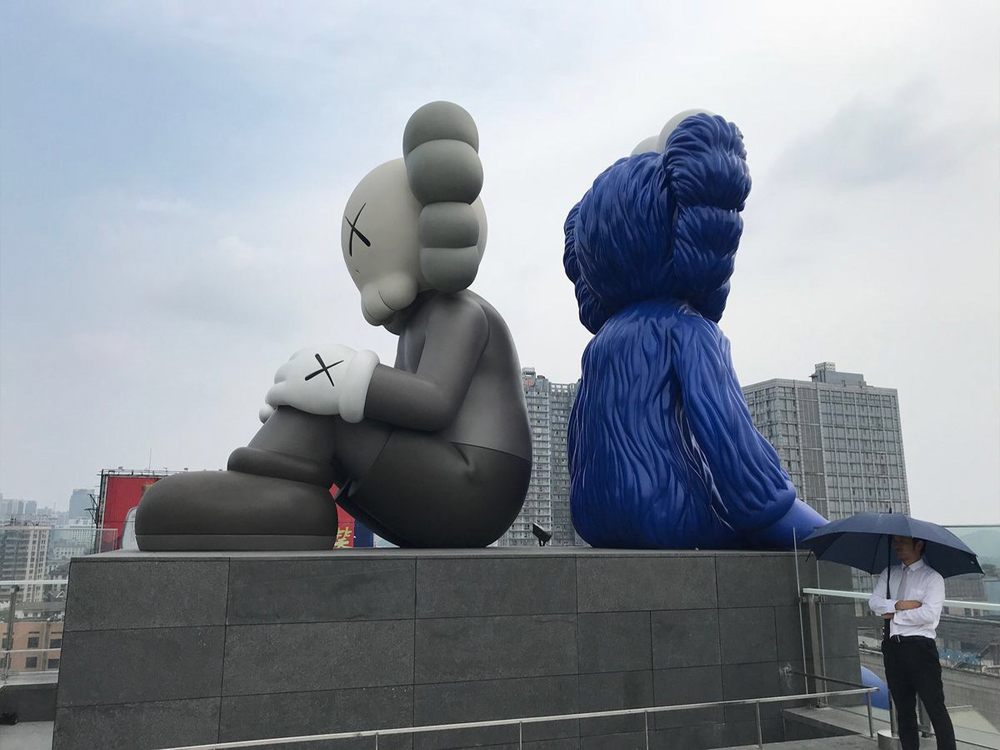
Creating porcelain sculptures with kinetic or moving components presents a unique set of challenges that blend artistry with engineering. Porcelain, known for its delicate beauty, is inherently fragile, making it difficult to incorporate moving parts without compromising structural integrity. The material's brittleness requires meticulous design to ensure that joints and hinges can withstand repeated motion without cracking or breaking.
Another challenge lies in the firing process. Porcelain must be fired at high temperatures, which can warp or distort carefully engineered moving components. Artists often need to experiment with multiple firings or alternative materials for movable parts, adding complexity to the creative process.
Balancing aesthetics and functionality is also critical. Kinetic porcelain sculptures must maintain their visual appeal while ensuring smooth, reliable movement. This demands precise craftsmanship and often innovative solutions, such as hidden mechanisms or lightweight designs.
Lastly, the interplay of weight and balance poses a challenge. Porcelain's density can make kinetic sculptures top-heavy or unstable, requiring careful calculation to achieve harmonious motion. Despite these hurdles, the result—a delicate yet dynamic porcelain masterpiece—is a testament to the artist's skill and patience.