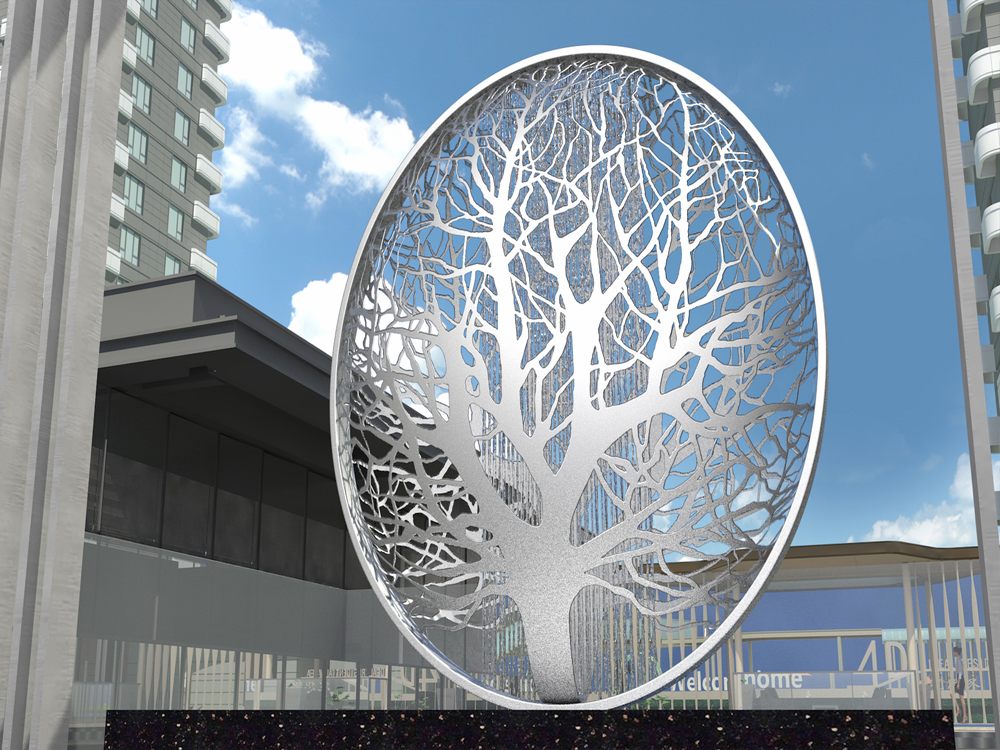
Creating porcelain sculptures with embedded lighting presents a fascinating intersection of traditional craftsmanship and modern technology, but this fusion comes with significant challenges. The delicate nature of porcelain, known for its fragility and translucent beauty, complicates the integration of electrical components. Artists must carefully balance the sculpture's structural integrity with the need to conceal wiring and power sources, often requiring innovative hollow designs that maintain the piece's aesthetic appeal while accommodating technical elements.
Thermal management poses another critical challenge, as traditional incandescent lighting generates heat that can damage porcelain or create stress points. This has led most contemporary artists to adopt cool-running LED solutions, though these still require careful placement to prevent light leakage or uneven illumination that might compromise the sculpture's visual harmony.
The firing process itself presents unique obstacles, as porcelain typically requires kiln temperatures exceeding 1,200°C – far beyond what electronic components can withstand. This necessitates a post-firing assembly approach where lighting elements are inserted after the final glaze firing, demanding precise pre-planning of cavities and access points during the sculpting phase.
Electrical safety remains paramount, especially for pieces intended to hold water or be displayed outdoors. Artists must master waterproofing techniques and comply with international safety standards while maintaining the sculpture's artistic vision. The marriage of these technical requirements with artistic expression continues to push the boundaries of what's possible in illuminated ceramic art.