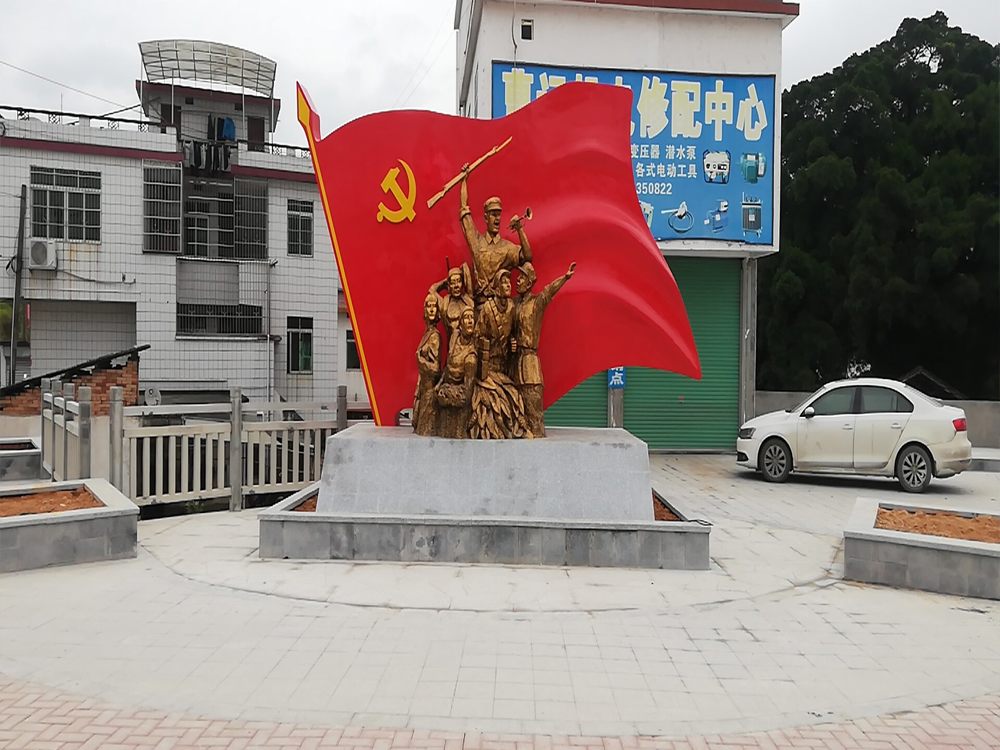
Porcelain sculptures, while beautiful, often face several common defects during production. Understanding these issues and their solutions ensures higher quality ceramic artworks.
1. Cracking: The most frequent defect occurs due to uneven drying or rapid temperature changes in the kiln. Artisans prevent this by controlling drying conditions and using grog (pre-fired clay particles) to improve clay stability.
2. Glaze defects: These include crawling (when glaze separates), pinholing, or blistering. Solutions involve precise glaze formulation, proper application thickness, and controlled kiln firing cycles.
3. Warping: Caused by uneven wall thickness or improper support during firing. Sculptors address this through balanced design and using kiln furniture for support.
4. Color inconsistencies: Result from uneven glaze application or kiln hotspots. Modern studios use computerized kilns and standardized glaze mixing to maintain color uniformity.
5. Structural weaknesses: Thin protruding parts often break. Artists reinforce these areas with internal supports or design modifications.
Advanced production techniques now incorporate digital modeling to predict stress points before creation. Many studios also implement quality control checkpoints at each production stage, from clay preparation to final firing.
Contemporary artists combine traditional craftsmanship with scientific understanding of materials to minimize defects. The porcelain sculpture field continues evolving with new materials and technologies that reduce production flaws while maintaining artistic integrity.