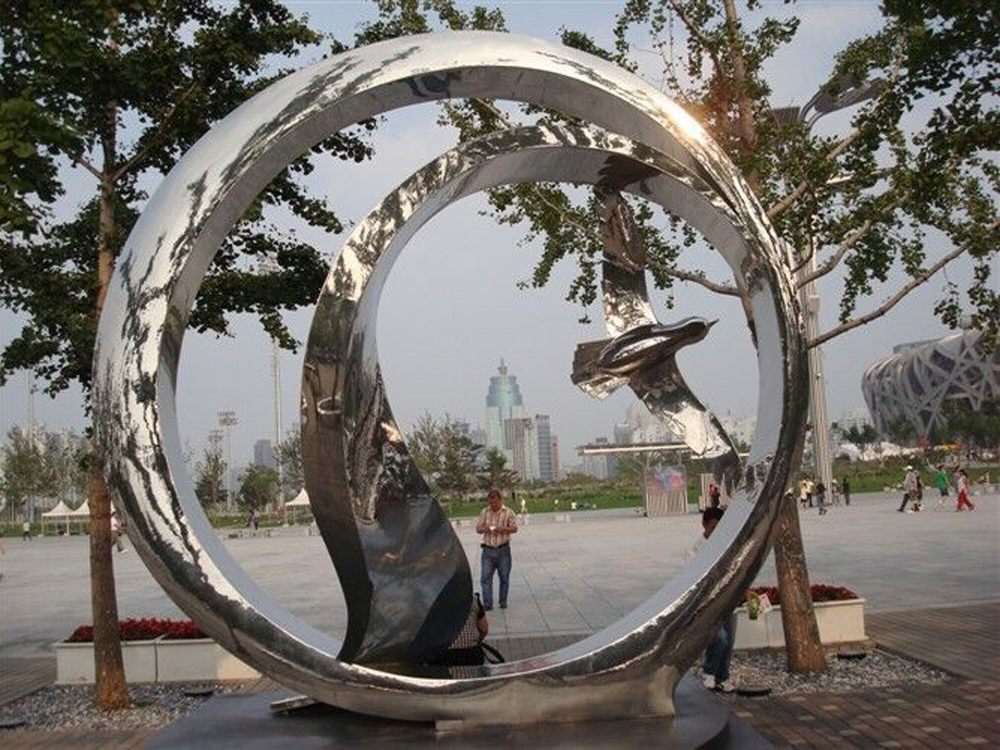
Creating porcelain sculptures with intricate undercuts is a demanding art form that tests the limits of both material and artist. Porcelain's inherent fragility poses the first major challenge, as thin or deeply undercut sections are prone to cracking during shaping or drying. The delicate nature of these designs requires exceptional skill in handling, as even slight pressure can ruin hours of meticulous work.
Firing presents another critical hurdle. As porcelain shrinks significantly during kiln exposure (typically 12-15%), complex undercuts may warp or collapse entirely. Artists must carefully calculate shrinkage rates and often create internal support structures that will burn away during firing. The high temperatures needed for vitrification (1280-1400°C) further complicate matters, as thermal stresses can cause unexpected fractures in delicate areas.
Technical execution demands innovative approaches. Traditional sculpting tools often prove inadequate for deep undercuts, forcing artists to develop custom implements or work in multiple assembled pieces. Surface finishing becomes exponentially more difficult in hard-to-reach areas, potentially compromising the sculpture's aesthetic unity.
Despite these challenges, successful undercut porcelain works display breathtaking artistry. Mastering these difficulties requires years of experience, patience with trial-and-error processes, and deep understanding of ceramic material science. Contemporary artists continue pushing boundaries by combining ancient techniques with modern technologies like 3D-printed supports or computer-aided design simulations to overcome these obstacles.