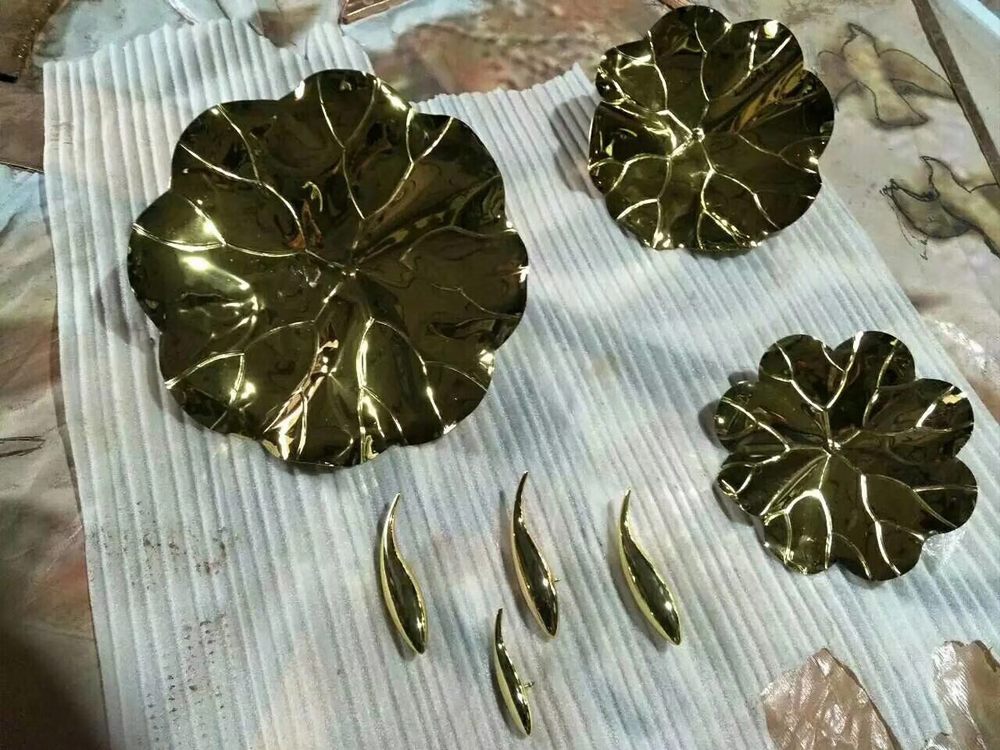
Creating porcelain sculptures with integrated kinetic mechanisms presents a fascinating yet demanding intersection of art and engineering. One of the primary challenges lies in the inherent fragility of porcelain, a material prized for its delicate beauty but prone to cracking under stress. Artists must carefully balance aesthetic vision with structural integrity, often requiring reinforced joints or specialized firing techniques.
The integration of movement introduces further complexity. Kinetic mechanisms demand precision engineering, which clashes with porcelain's unpredictable behavior during firing and cooling. Thermal expansion differences between ceramic and metal components can cause failures, necessitating innovative solutions like ceramic bearings or flexible connectors.
Additionally, the weight distribution of moving parts must be meticulously calculated to prevent strain on thin porcelain sections. This often limits the scale and complexity of kinetic elements, pushing artists to develop minimalist yet expressive motion systems. The final challenge emerges in maintenance—porcelain's brittleness makes repairs nearly impossible, requiring flawless initial execution.
Despite these hurdles, successful kinetic porcelain sculptures achieve a mesmerizing harmony of fragility and motion, pushing the boundaries of contemporary ceramic art.