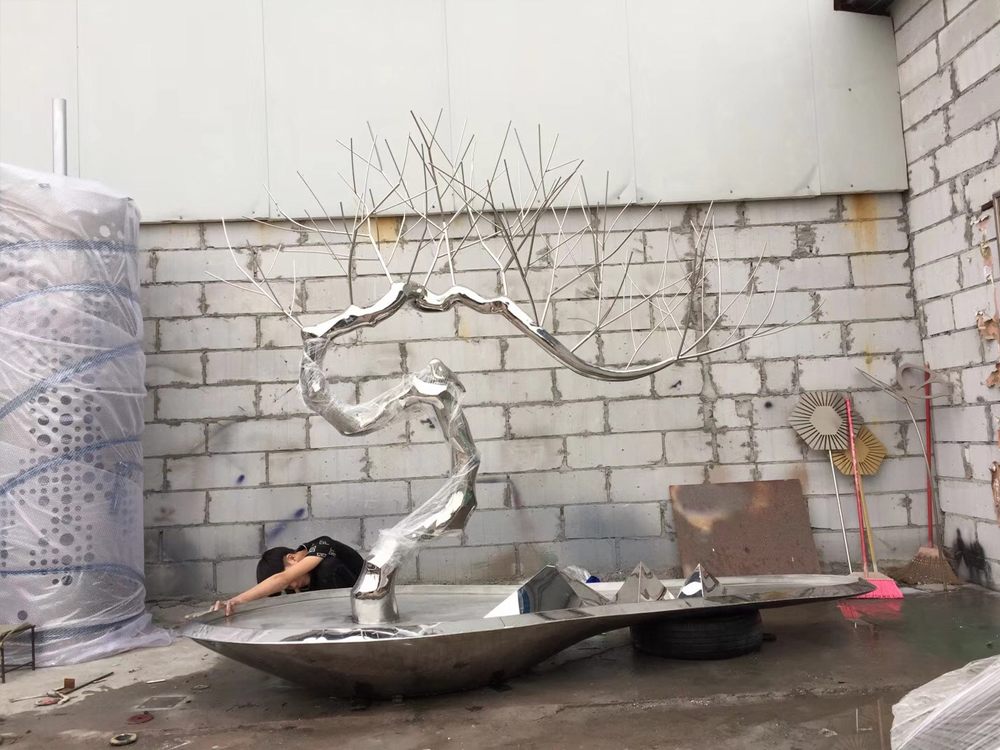
Creating porcelain sculptures with integrated mechanical components is a fascinating yet demanding art form that merges delicate ceramic craftsmanship with precise engineering. One of the primary challenges lies in the fragility of porcelain, which can crack or shatter during the sculpting or assembly process, especially when paired with rigid mechanical parts. The differing thermal expansion rates of porcelain and metal components also pose a risk, as firing the sculpture in a kiln may cause stress fractures or misalignment.
Additionally, achieving seamless integration requires meticulous planning. The mechanical elements must be designed to complement the porcelain’s aesthetic without compromising its structural integrity. Weight distribution is another critical factor, as unbalanced components can lead to instability or collapse.
Artists must also consider the long-term durability of such hybrid pieces. Porcelain is prone to wear over time, while mechanical parts may corrode or degrade, requiring careful material selection and protective treatments. Despite these hurdles, the fusion of porcelain and mechanics offers unparalleled creative possibilities, pushing the boundaries of traditional ceramic art.