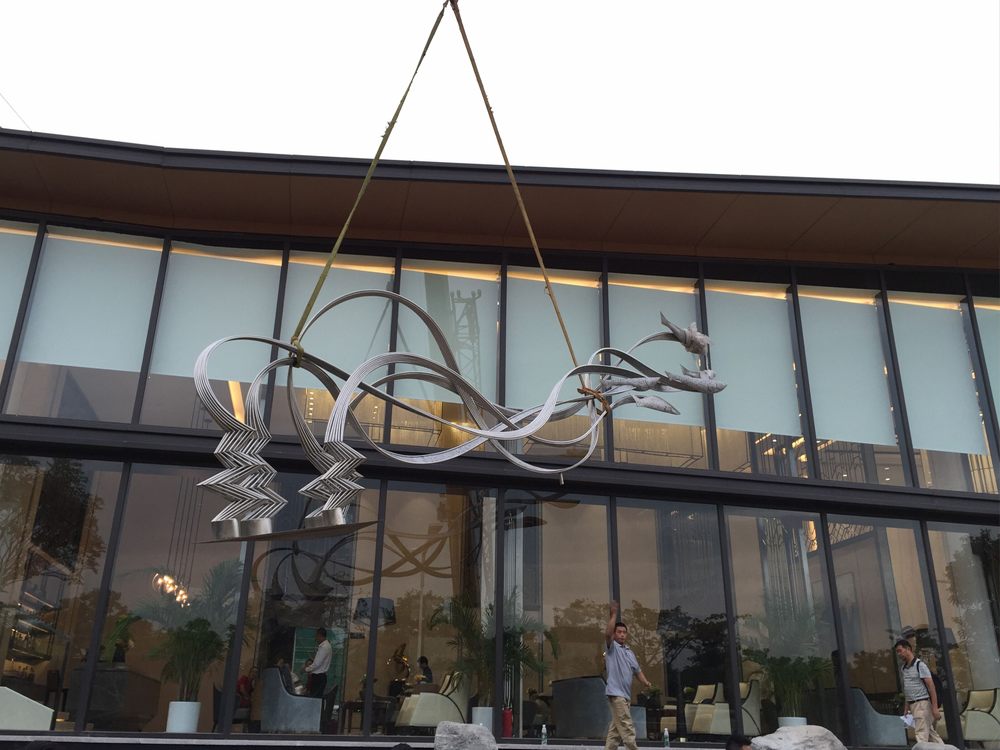
Creating porcelain sculptures with delicate, free-hanging elements is a testament to an artist’s skill and patience. These intricate designs demand a deep understanding of ceramic materials and precise techniques to ensure stability without compromising aesthetics.
Artists begin by carefully selecting high-quality porcelain clay, known for its fine texture and strength when fired. The clay must be meticulously shaped, often using supportive armatures or temporary structures to hold free-hanging parts in place during drying and firing.
Firing is a critical stage. Porcelain shrinks significantly, so artists calculate shrinkage rates to avoid warping or cracking. Some use multiple low-temperature firings to gradually strengthen delicate sections before the final high-temperature firing.
Innovative approaches include incorporating hidden supports or designing interlocking elements that provide internal stability. Others employ slip-casting or 3D printing to achieve complex geometries with uniform thickness, reducing weak points.
The result is breathtaking sculptures where seemingly fragile elements defy gravity, showcasing the artist’s mastery of material and form. This delicate balance of art and engineering continues to push the boundaries of ceramic artistry.