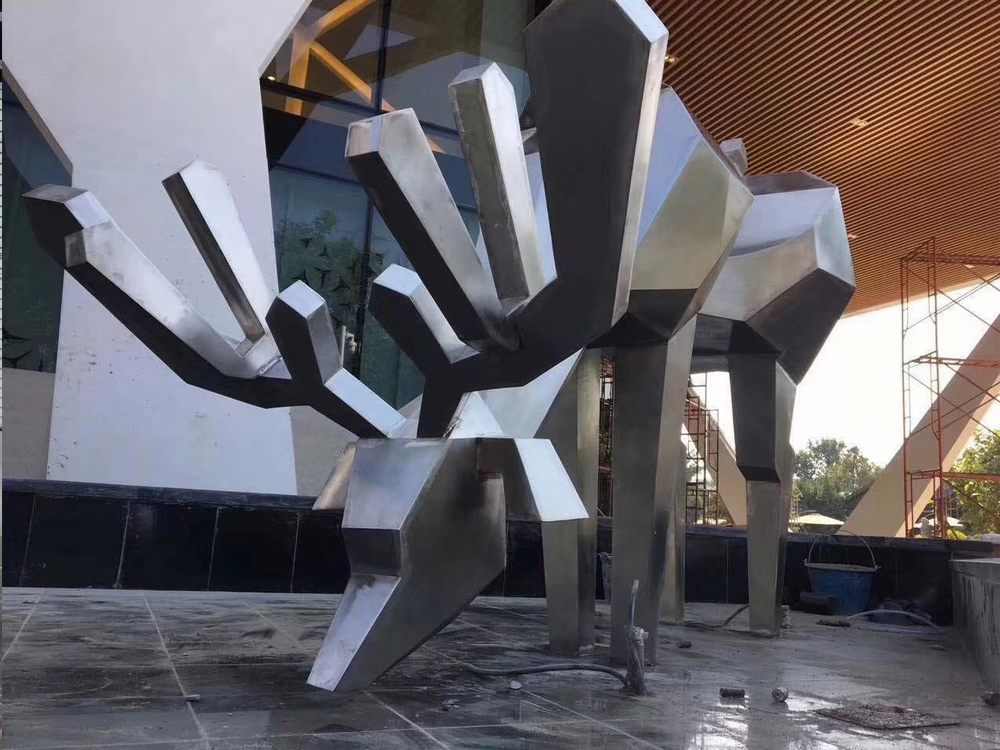
The integration of automation into porcelain sculpture component manufacturing is revolutionizing an ancient art form. Advanced technologies like robotic clay shaping and AI-guided kiln firing systems are achieving micron-level precision unattainable through traditional handcrafting methods. This shift enables mass production of intricate components while maintaining artistic integrity, fundamentally altering the economics of ceramic art.
3D printing emerges as a game-changer, allowing artists to prototype complex geometries in porcelain that would collapse under conventional wheel-throwing techniques. Industrial robotic arms equipped with pressure-sensitive tools now replicate master sculptors' touch, producing identical components for large installations with perfect consistency.
However, this technological leap presents challenges. The loss of subtle handcrafted variations raises philosophical questions about authenticity in ceramic art. Smaller studios face steep adoption barriers due to equipment costs, potentially widening the gap between industrial and artisanal producers.
Environmental implications prove equally significant. Automated kilns optimize energy use, reducing the carbon footprint of porcelain firing by up to 40%. Yet the disposal of ceramic support materials from automated processes requires new waste management solutions.
The most profound impact may be creative. Digital design tools coupled with automated production are giving rise to entirely new porcelain aesthetics - ultra-thin translucent structures and mathematically precise fractal patterns that redefine the boundaries of ceramic art. As the technology matures, the dialogue between human creativity and machine precision continues to shape the future of porcelain sculpture.