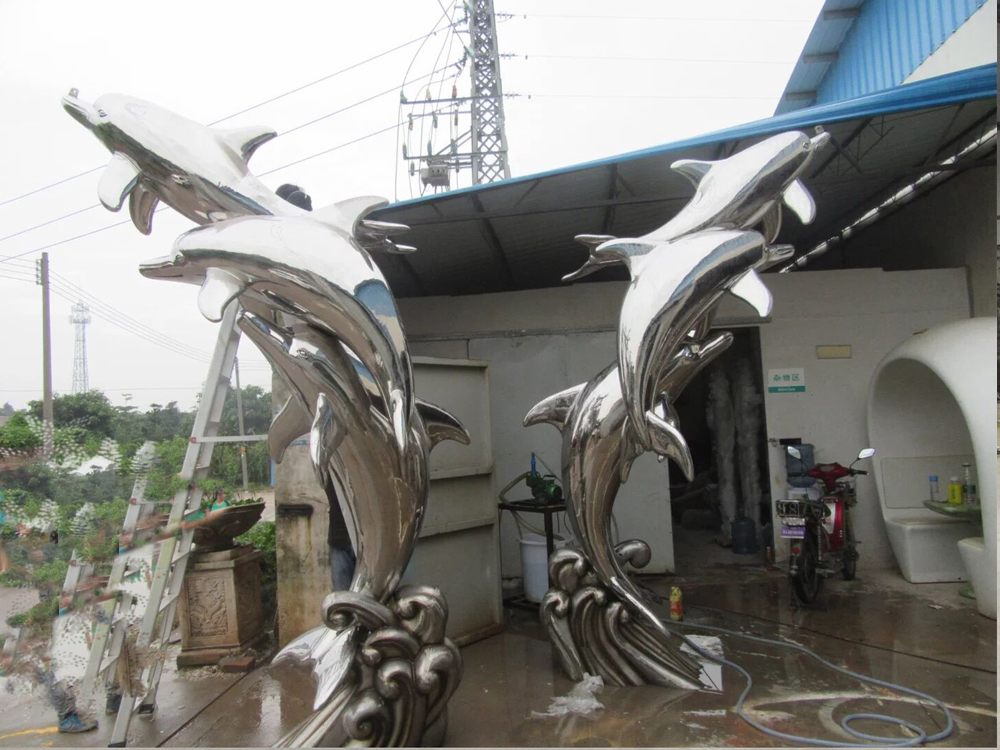
Creating porcelain sculptures with thin, delicate components requires a blend of artistic vision and scientific precision. Artists employ several key techniques to ensure structural integrity:
1. Clay Composition Optimization
Specialized porcelain blends with added kaolin or ball clay increase plasticity while maintaining strength. Many artists create custom clay bodies with precisely calculated shrinkage rates to prevent warping.
2. Strategic Armature Systems
Internal support structures made of high-temperature wires or ceramic rods provide hidden reinforcement. These are often designed to melt or integrate seamlessly during firing.
3. Controlled Drying Processes
Multi-stage drying using humidity chambers prevents stress fractures. Critical joints may be wrapped in damp cloths to ensure even moisture evaporation.
4. Engineering Through Design
Smart geometry incorporates natural arches and weight-distributing curves. Hollow construction with uniform wall thickness prevents collapse during firing.
5. Precision Firing Techniques
Custom kiln programs with extended bisque firings and precisely controlled cooling cycles minimize thermal shock. Some artists use multiple lower-temperature firings for vulnerable elements.
6. Reinforcement Innovations
Contemporary methods include ceramic fiber additives, nano-particle infusions, and post-firing resin treatments for particularly fragile areas.
The most successful pieces balance aesthetic delicacy with hidden structural intelligence - proving that in porcelain art, true fragility is often an illusion of masterful engineering.