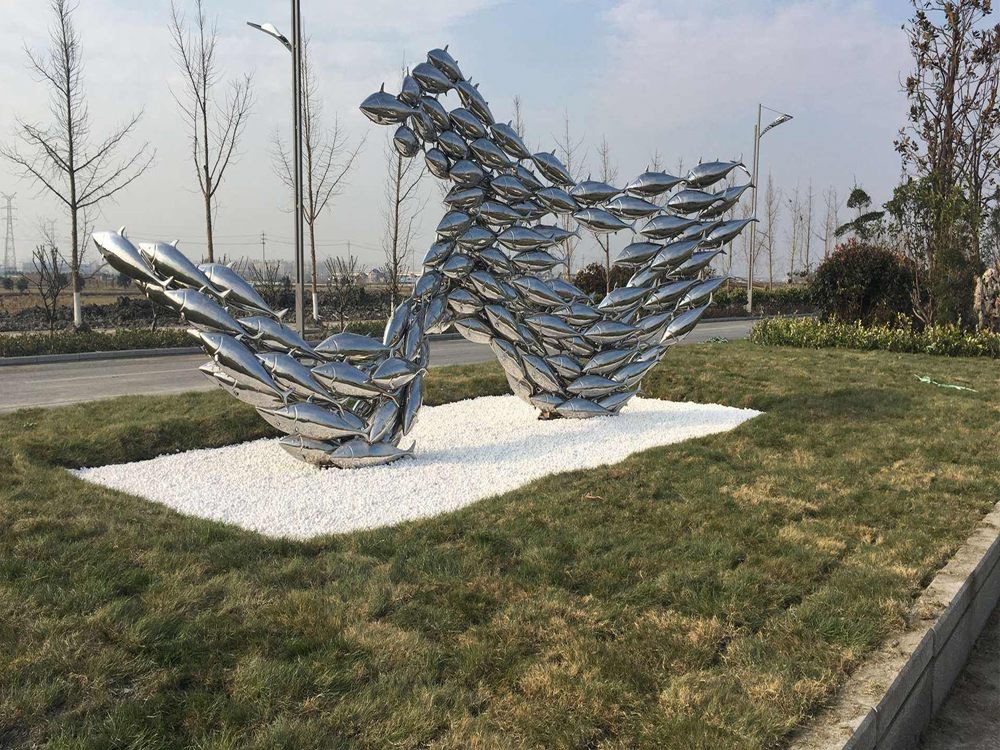
Creating porcelain sculptures with hollow interiors is a delicate art form that demands precision, patience, and innovative techniques. Artists face several challenges, including structural integrity, drying and firing risks, and maintaining intricate details.
To ensure stability, sculptors often use coil-building or slip-casting methods, carefully layering clay to form hollow sections while avoiding collapse. Internal supports, like paper or foam, are temporarily inserted during shaping and removed before firing.
Drying is a critical phase—uneven shrinkage can cause cracks. Artists control humidity and airflow, sometimes covering pieces with plastic to slow moisture loss. Kiln firing presents another hurdle; rapid temperature changes may warp or shatter the sculpture. Gradual heating and cooling cycles are essential.
Innovations like 3D-printed molds or hybrid clay formulas enhance durability. Mastery of these techniques allows artists to produce breathtaking hollow porcelain works, blending fragility with strength in timeless ceramic art.