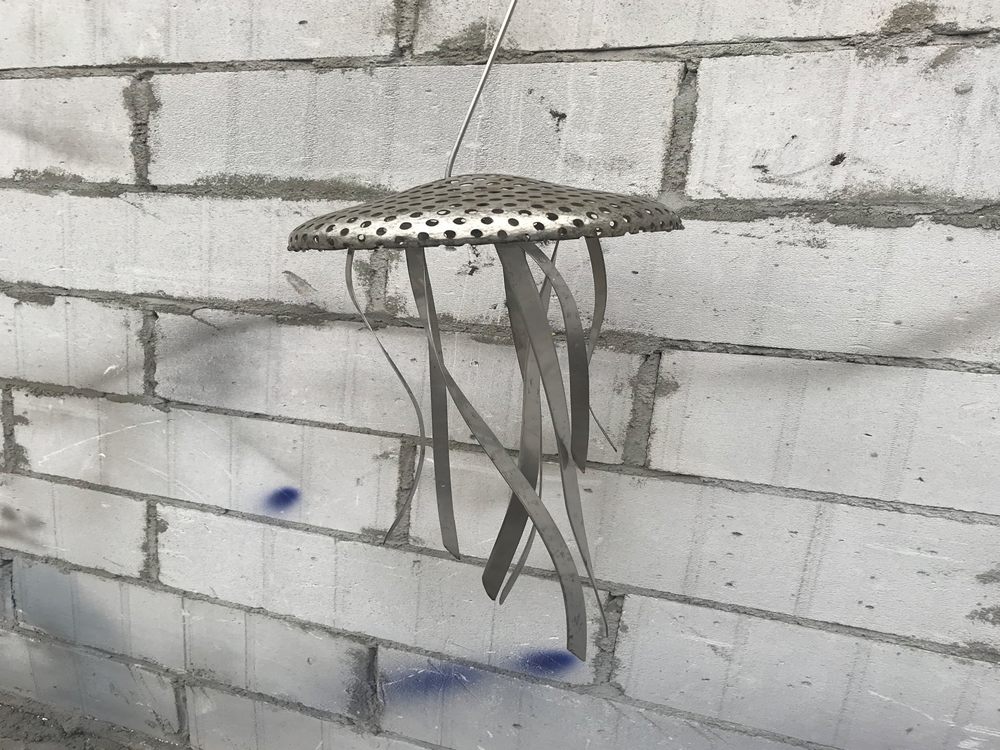
Creating bronze sculptures with delicate, thin elements presents unique artistic and technical hurdles. One major challenge is achieving structural integrity—thin bronze sections are prone to cracking or warping during cooling. The casting process itself demands precision; molten bronze’s high viscosity struggles to fill intricate molds, often resulting in incomplete details.
Thermal stress poses another obstacle. Uneven cooling between thick and thin sections causes internal tensions, requiring controlled annealing processes. Finishing work becomes exponentially harder—polishing or patinating fragile areas risks breakage, demanding specialized tools and patience.
Material limitations also emerge. While bronze alloys vary, most shrink 2-3% during solidification, distorting fine features. Artists combat this through wax mold adjustments or post-casting cold working. Environmental factors compound these issues—temperature fluctuations can fatigue thin metal over time.
Successful solutions include:
- Using silicon bronze for better flow characteristics
- Implementing multi-piece molds for complex geometries
- Applying reinforcement rods in wax originals
- Adopting incremental welding techniques for repairs
Master sculptors emphasize prototyping with 3D-printed models and employing lost-wax casting variations like ceramic shell for superior detail capture. The balance between aesthetic vision and metallurgical reality defines exceptional bronze artistry.