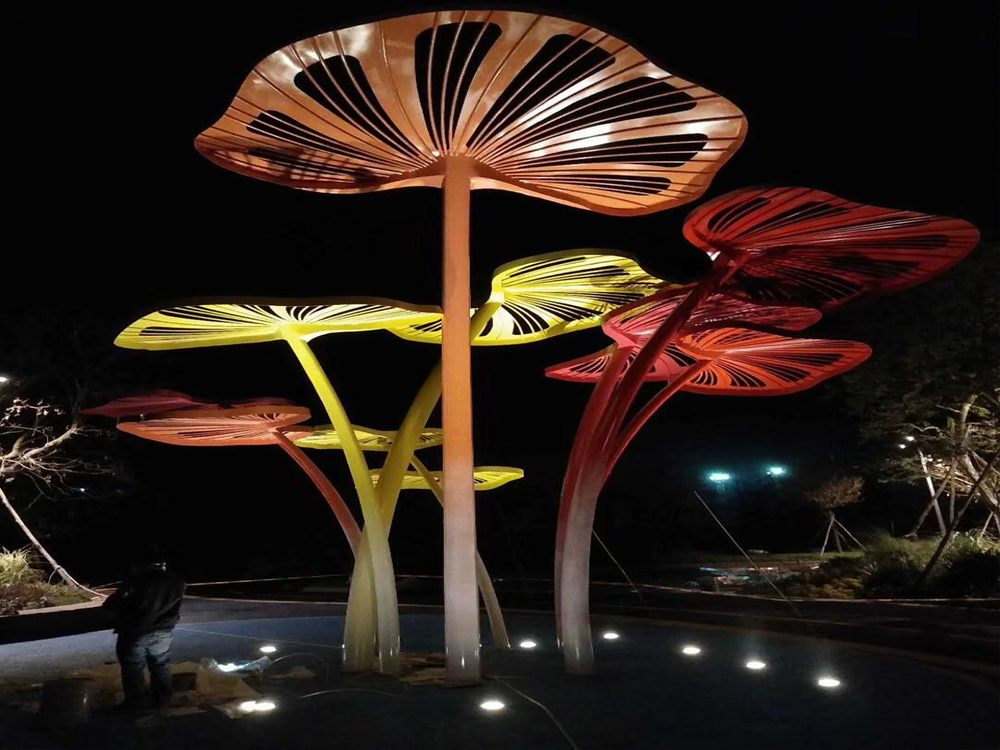
Lost-wax casting, also known as investment casting, is a meticulous process that relies heavily on the quality and type of wax used to create patterns. The wax must exhibit specific properties, such as low ash content, high dimensional stability, and ease of removal. Here are the most common types of wax used in this process:
1. Microcrystalline Wax: Known for its flexibility and fine grain structure, this wax is ideal for intricate designs. It melts at higher temperatures, reducing the risk of deformation during handling.
2. Paraffin Wax: A cost-effective option, paraffin wax is often blended with other waxes to improve its performance. It’s easy to carve but requires additives for better strength.
3. Beeswax: Traditionally used in ancient casting, beeswax offers excellent workability and a natural adhesive quality. However, it’s less common in modern foundries due to its higher cost.
4. Synthetic Wax: Engineered for precision, synthetic waxes provide superior consistency and are often used in high-volume production. They minimize shrinkage and ensure repeatability.
5. Pattern Wax: Specifically formulated for lost-wax casting, this wax combines multiple wax types to balance malleability and durability, making it a favorite among jewelers and sculptors.
Each type of wax has unique advantages, and the choice depends on the project’s requirements, such as detail level, production scale, and budget. Understanding these options ensures optimal results in the lost-wax casting process.