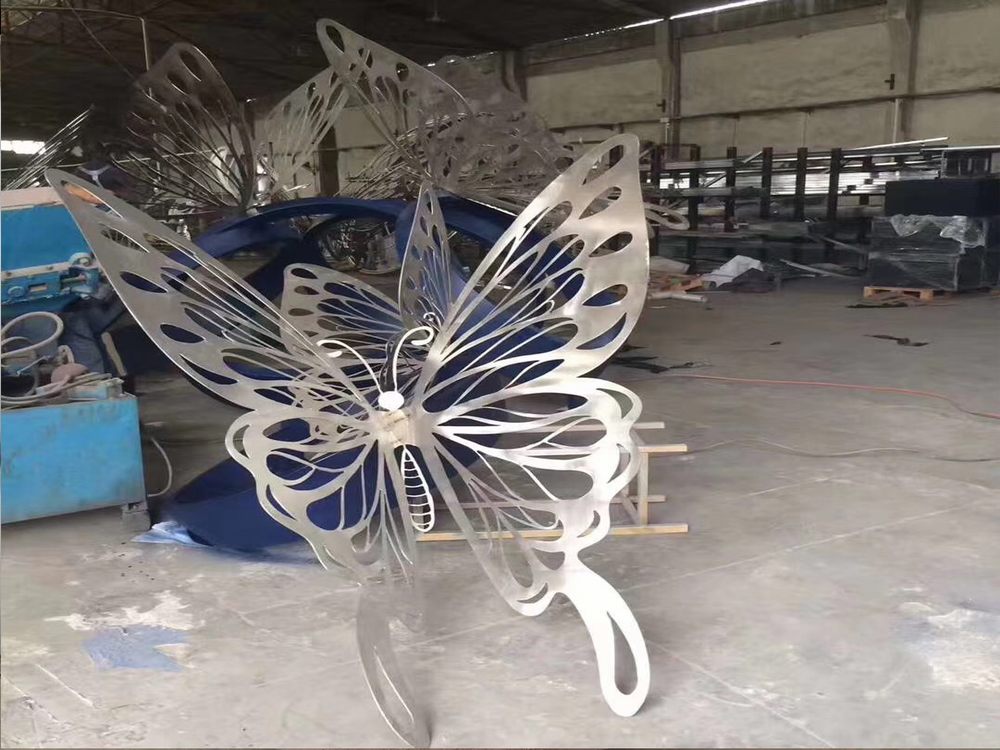
Lost-wax casting, a centuries-old metalworking technique, is widely used for creating intricate metal parts. Two primary methods dominate this process: direct and indirect lost-wax casting. Understanding their differences helps artisans and manufacturers choose the right approach for their projects.
Direct Lost-Wax Casting
In the direct method, the artist sculpts the final object directly in wax. This wax model is then invested in a ceramic shell, burned out, and replaced with molten metal. This approach offers greater artistic freedom since the wax can be manipulated freely without intermediate steps. Jewelry makers and sculptors often prefer this method for one-of-a-kind pieces where fine details matter most.
Indirect Lost-Wax Casting
The indirect method introduces an intermediate step: creating a master pattern (usually in metal or resin) first. From this master, a mold is made to produce multiple wax copies. These wax replicas then undergo the standard investment casting process. This method excels in mass production scenarios where consistency across multiple copies is crucial. Industrial applications and jewelry manufacturers frequently use this approach.
Key Differences
1. Process Complexity: Direct casting is simpler with fewer steps, while indirect casting requires additional pattern-making stages.
2. Reproduction: Indirect methods allow for identical reproductions; direct methods create unique pieces.
3. Cost Efficiency: Indirect becomes cost-effective for large quantities despite higher initial setup costs.
4. Detail Preservation: Direct casting better preserves ultra-fine details since it avoids mold-making that might compromise intricacy.
5. Material Choices: Indirect methods often use more durable master patterns to withstand repeated mold-making.
Modern applications leverage both methods - direct for artistic pieces and prototypes, indirect for production runs. Technological advancements like 3D printing are blurring these traditional distinctions, offering new hybrid approaches in investment casting.
Choosing between these methods depends on your project requirements regarding quantity, detail level, and budget constraints. Both continue to play vital roles in metal casting across industries from aerospace to fine art.