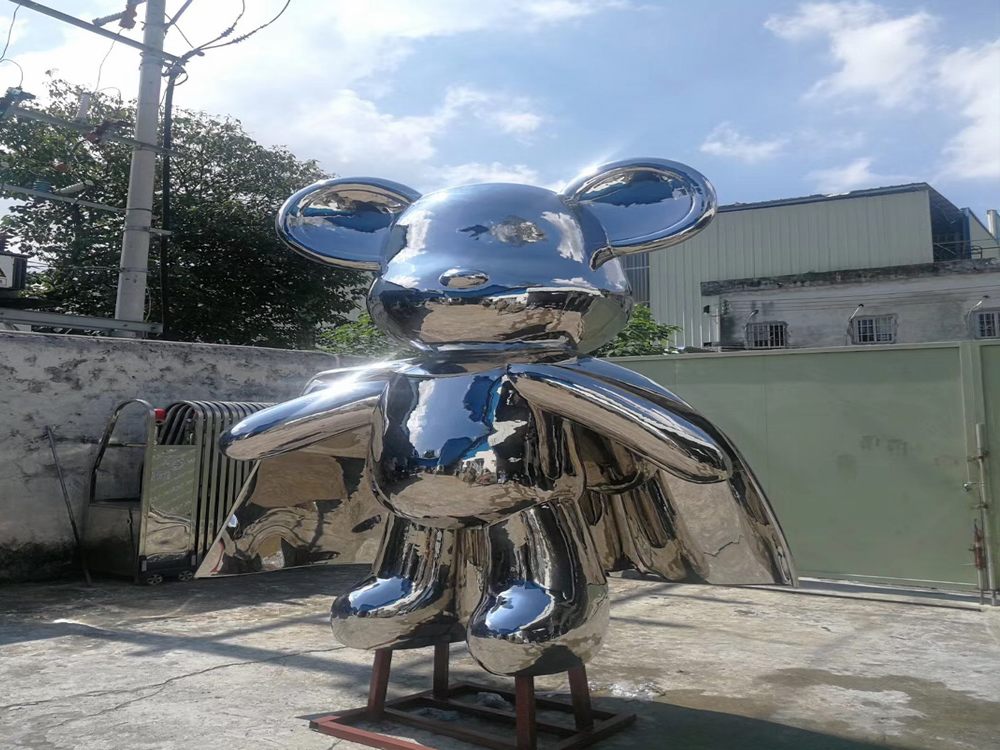
The rise of CNC (Computer Numerical Control) machines has sparked a fascinating evolution in wood carving, blending centuries-old craftsmanship with cutting-edge technology. While traditional hand carving relies on artisan skill, patience, and intimate material knowledge, CNC routers offer unprecedented precision, repeatability, and efficiency in woodworking.
Modern CNC technology excels at producing complex geometric designs and flawless reproductions that would take master carvers weeks to complete. This has democratized access to intricate woodwork, allowing furniture makers and decor manufacturers to maintain consistent quality at scale. However, purists argue that machine-carved pieces lack the soul, subtle imperfections, and tactile warmth of handcrafted work.
The most significant impact lies in hybrid approaches. Many contemporary artisans now use CNC for rough shaping and repetitive elements, reserving hand tools for final detailing. This fusion preserves traditional techniques while embracing efficiency. Educational institutions have adapted by teaching both methodologies, ensuring new generations master foundational skills before exploring digital tools.
As sustainability gains importance, CNC's material optimization reduces waste compared to traditional methods. Yet the market still values handmade pieces at premium prices, suggesting both techniques will coexist. The future likely holds augmented reality-assisted carving and AI-driven CNC systems that mimic artisan decision-making – further blurring the line between machine precision and human artistry.
Ultimately, CNC hasn't replaced traditional carving but has redefined its context. The technology handles production demands while freeing artisans to focus on truly unique, creative expressions that machines cannot replicate. This symbiotic relationship continues to push woodworking into exciting new territories while honoring its rich heritage.