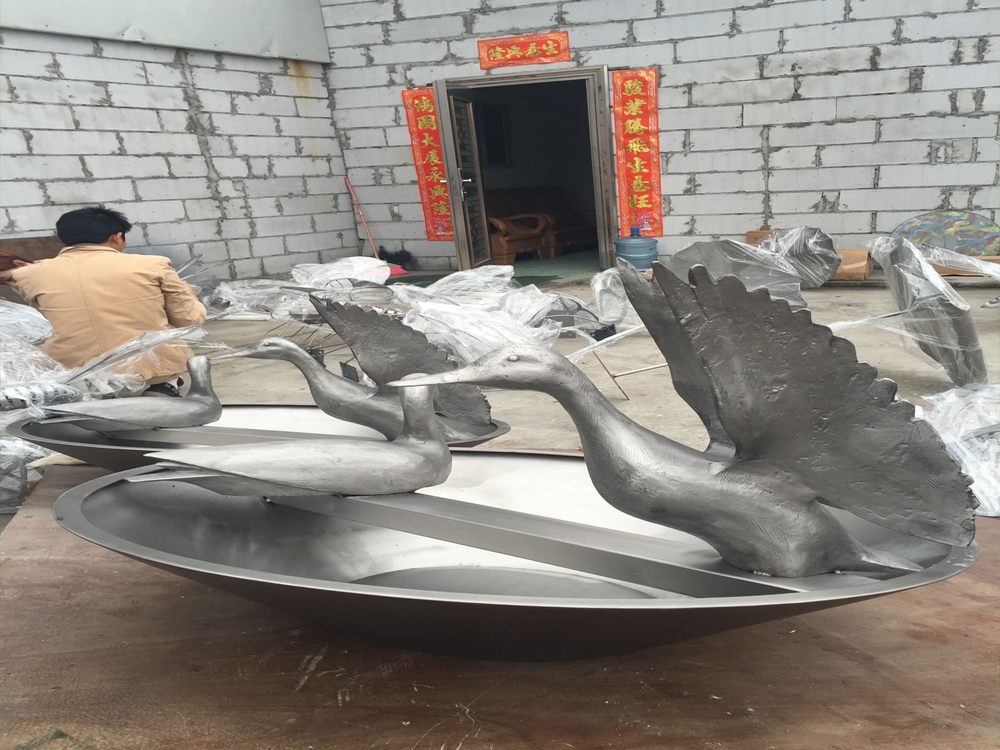
The firing temperature plays a pivotal role in determining the durability and aesthetic finish of porcelain sculptures. When clay is subjected to high temperatures in a kiln, its molecular structure undergoes vitrification, transforming it into a dense, glass-like material. Higher firing temperatures (typically between 1200°C and 1400°C) enhance durability by reducing porosity, making the sculpture less susceptible to moisture absorption and mechanical stress. However, excessively high temperatures can cause warping or cracking, compromising structural integrity.
The finish of porcelain sculptures is equally influenced by firing conditions. Lower temperatures (below 1100°C) result in a matte, porous surface, while mid-range firings (1100°C–1200°C) produce a semi-vitreous finish. At peak temperatures, glazes mature fully, creating a glossy, impermeable surface that enhances both visual appeal and longevity. Artists must balance temperature control with clay composition and glaze chemistry to achieve the desired balance of strength and beauty.
Understanding these dynamics allows ceramicists to optimize their kiln settings, ensuring their porcelain sculptures withstand time while showcasing exquisite craftsmanship.