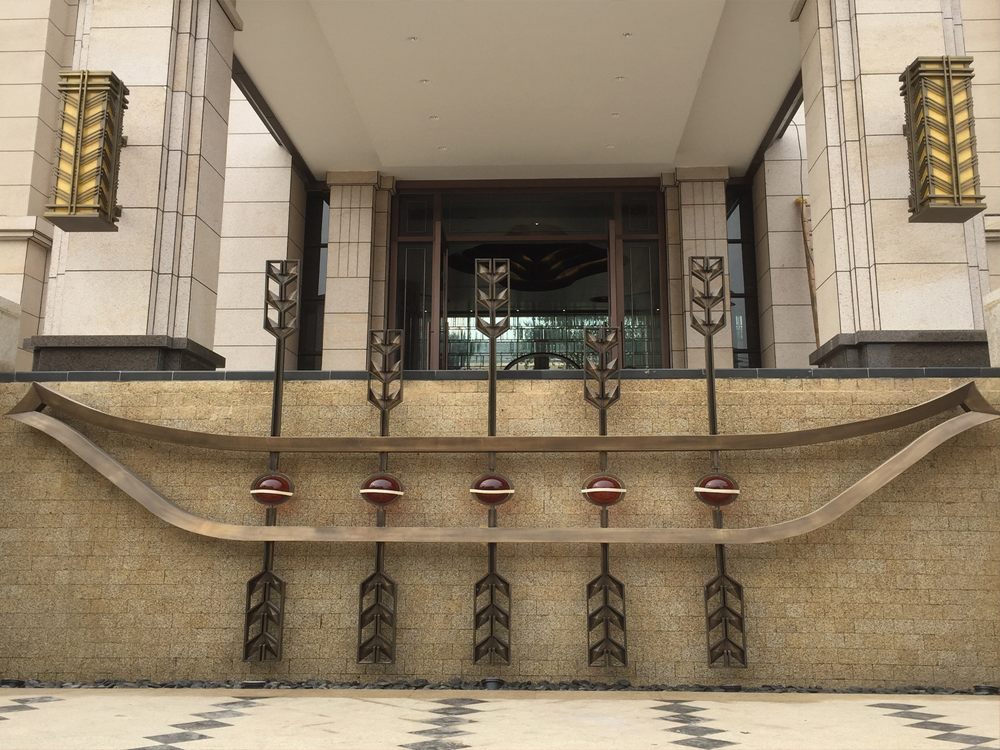
Porcelain sculptures are delicate artworks that require precise firing conditions to avoid defects like cracking or warping. One of the most frequent causes is rapid temperature changes during heating or cooling, which creates internal stress in the clay. If the kiln temperature rises or drops too quickly, the uneven expansion or contraction leads to fractures.
Another major factor is improper clay composition. Porcelain must have the right balance of kaolin, feldspar, and quartz to maintain stability. Impurities or incorrect ratios weaken the structure, making it prone to warping under high heat.
Inadequate drying before firing is also a common issue. If moisture remains trapped inside the sculpture, it turns to steam during firing, causing cracks or even explosions. Slow, even drying is essential to prevent this.
Additionally, kiln placement matters. If sculptures are too close to heating elements or stacked improperly, uneven heat distribution can cause warping. Proper spacing and kiln shelf preparation help maintain consistent temperatures.
Lastly, firing schedule errors—such as incorrect peak temperatures or insufficient soaking time—can lead to underfired or overfired porcelain, increasing the risk of structural failure. A well-calibrated kiln and controlled firing cycle are critical for flawless results.
By addressing these common issues, artists can minimize defects and achieve beautifully fired porcelain sculptures.