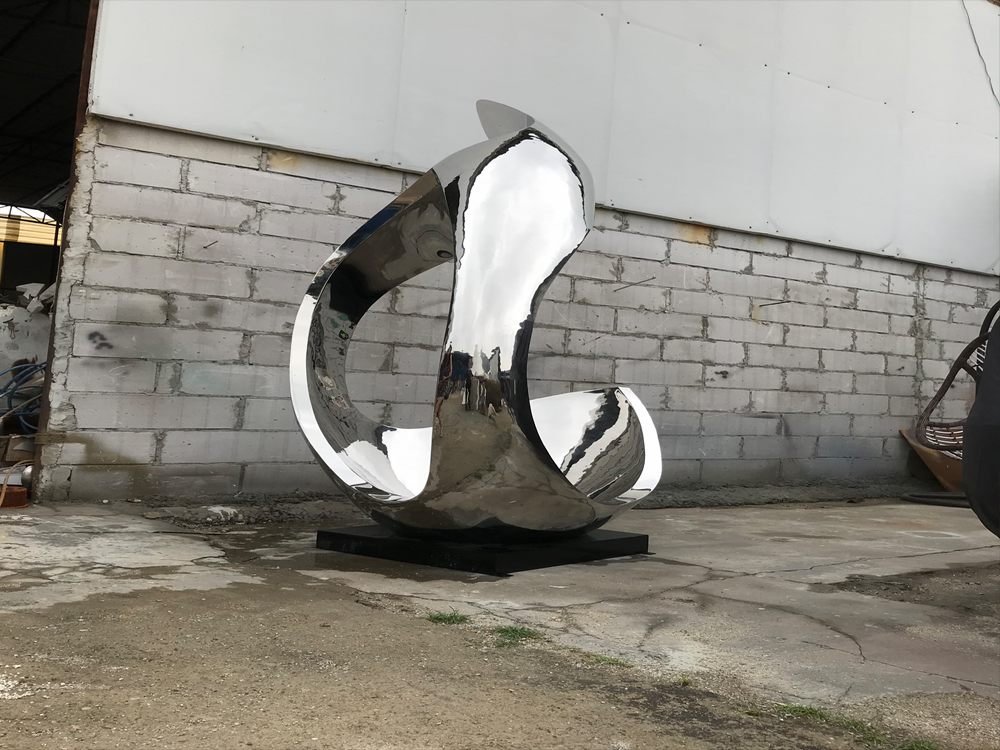
Creating porcelain sculptures with extreme surface porosity presents unique artistic and technical challenges. The delicate nature of porcelain clay, combined with intentional porosity, demands meticulous craftsmanship at every stage.
Material fragility is the primary hurdle. Porcelain's fine particle structure makes it prone to cracking during drying, especially when artists carve deep pores or thin-walled designs. The clay's low plasticity further complicates shaping, as porous surfaces require careful handling to maintain structural integrity.
Firing techniques become exponentially more complex. High kiln temperatures (typically 1200-1400°C) must be carefully controlled to prevent warping or collapse of the porous structure. Rapid temperature changes can cause thermal shock, creating invisible stress points that may lead to later fractures.
Glazing porous surfaces introduces additional challenges. The glaze may fill intended pores or create uneven coatings, requiring multiple test firings. Artists often develop specialized application methods, such as spray glazing or wax resist techniques, to preserve surface texture.
Long-term durability concerns persist even after successful firing. Porous areas accumulate dirt more readily and are more susceptible to moisture damage. Some artists address this with innovative sealing methods, though this risks altering the intended aesthetic.
Mastering these challenges requires deep material knowledge and experimental approaches. Many ceramic artists document years of trial and error before achieving consistent results with highly porous porcelain works. The reward lies in creating pieces that push the boundaries of ceramic art while maintaining structural soundness.