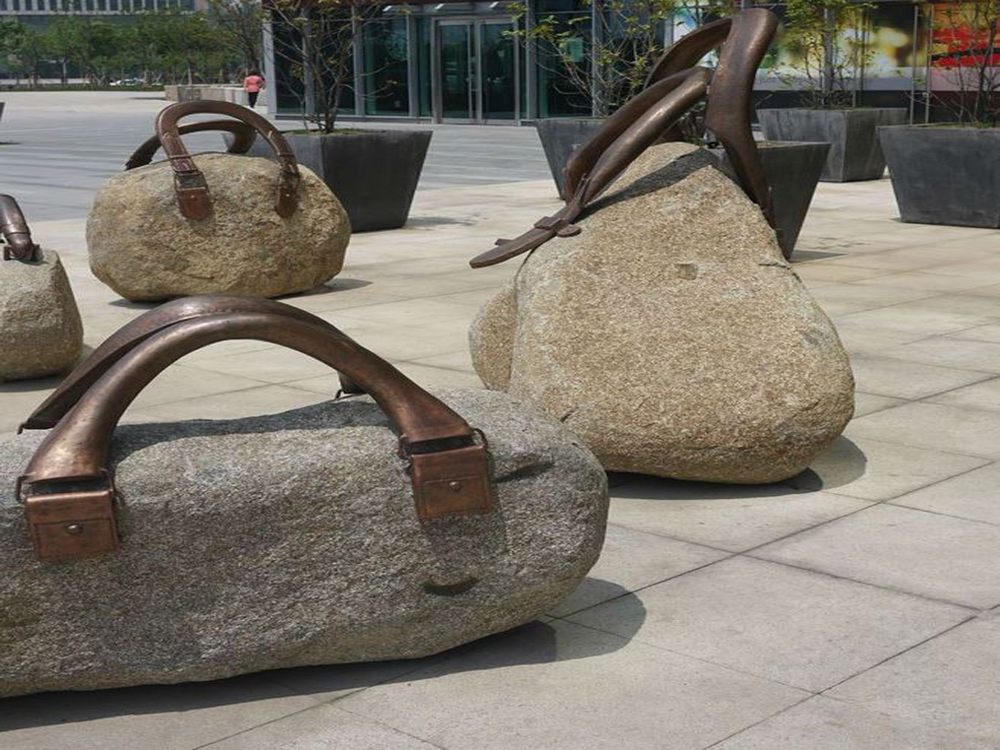
Creating porcelain sculptures with temperature-sensitive elements presents a unique set of challenges for ceramic artists. One of the primary difficulties lies in the kiln firing process, where precise temperature control is crucial. Porcelain requires high firing temperatures (often exceeding 1200°C), which can warp, crack, or melt delicate temperature-sensitive additions.
Material compatibility is another significant hurdle. Many decorative elements like metallic accents or glass inclusions have different thermal expansion rates than porcelain, leading to stress fractures during cooling. Artists must carefully select materials that can withstand the firing cycle or employ post-firing attachment methods, which often compromise structural integrity.
The drying phase before firing also poses risks. Porcelain's low plasticity makes it prone to cracking as moisture evaporates, and combined elements may dry at uneven rates. This demands meticulous timing and humidity control in the studio.
Additionally, achieving consistent results is exceptionally difficult. Minor variations in kiln atmosphere, heating rates, or cooling cycles can dramatically affect the final piece. Many artists face trial-and-error processes spanning dozens of attempts before perfecting their techniques.
Despite these challenges, successful integration of temperature-sensitive elements can yield breathtaking results, pushing the boundaries of ceramic art. The key lies in thorough material testing, controlled firing schedules, and embracing the unpredictable nature of porcelain as part of the creative process.