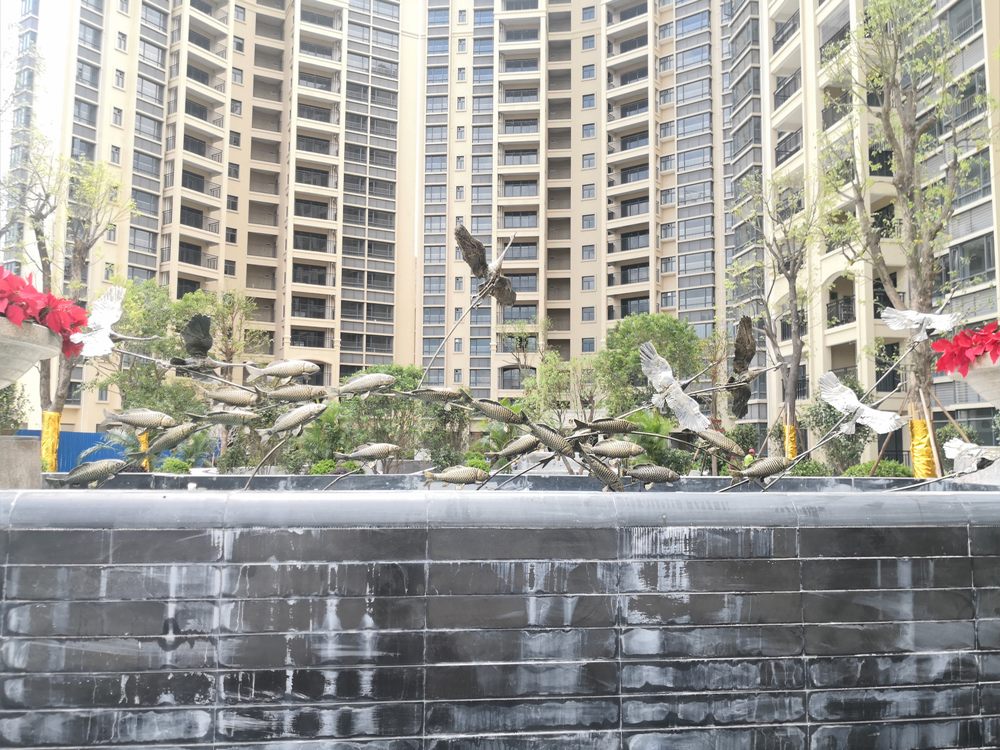
Creating porcelain sculptures with mixed material inclusions presents unique challenges for both artists and manufacturers. The delicate nature of porcelain, combined with the integration of diverse materials like metals, glass, or resins, requires meticulous planning and innovative techniques.
Artists often begin by testing material compatibility to avoid cracking or discoloration during firing. They may use low-fire porcelain or adjust kiln temperatures to accommodate mixed media. Some employ post-firing assembly, attaching non-ceramic elements after the porcelain has cooled to prevent thermal stress.
Manufacturers address production challenges by developing specialized adhesives and reinforcement methods. They might create custom molds that account for material expansion rates or use 3D printing to prototype complex hybrid designs. Advanced glazing techniques help unify the visual appearance of disparate materials.
Collaboration between artists and material scientists has led to breakthroughs like ceramic-metal composites that withstand firing temperatures. Others incorporate organic materials that burn away during firing, leaving intriguing textures. The key lies in balancing artistic vision with technical feasibility, pushing the boundaries of traditional porcelain craftsmanship while maintaining structural integrity.
Successful mixed-material porcelain works demonstrate how these challenges inspire creativity rather than limit it, resulting in sculptures that showcase the best qualities of each component material while achieving harmonious unity.