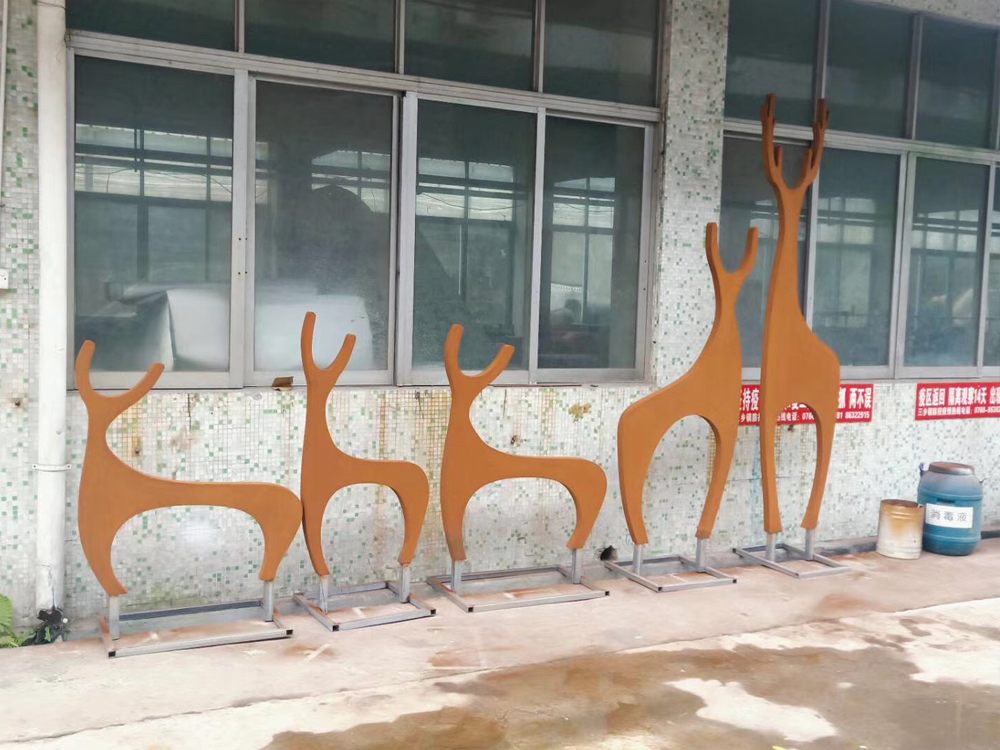
The world of porcelain sculpture prototyping is undergoing a revolution thanks to cutting-edge 3D printing innovations. One breakthrough is high-resolution ceramic 3D printing, enabling intricate details previously impossible with traditional methods. New multi-material printers now combine porcelain with supportive structures that dissolve post-printing, allowing for complex hollow designs.
Sustainable approaches are emerging, with recycled porcelain powders and bio-based binders reducing environmental impact. Advanced sintering techniques paired with 3D printing create stronger final products while maintaining delicate artistic qualities. Some systems now incorporate AI-assisted design optimization specifically for porcelain's unique properties during firing.
Perhaps most exciting is the development of hybrid machines that seamlessly transition from digital modeling to 3D printing to final kiln firing in one integrated process. These innovations are making porcelain prototyping faster, more precise, and accessible to smaller studios while preserving the material's timeless artistic qualities. The future promises even finer resolutions and smarter material systems that respond predictably to the challenges of porcelain work.