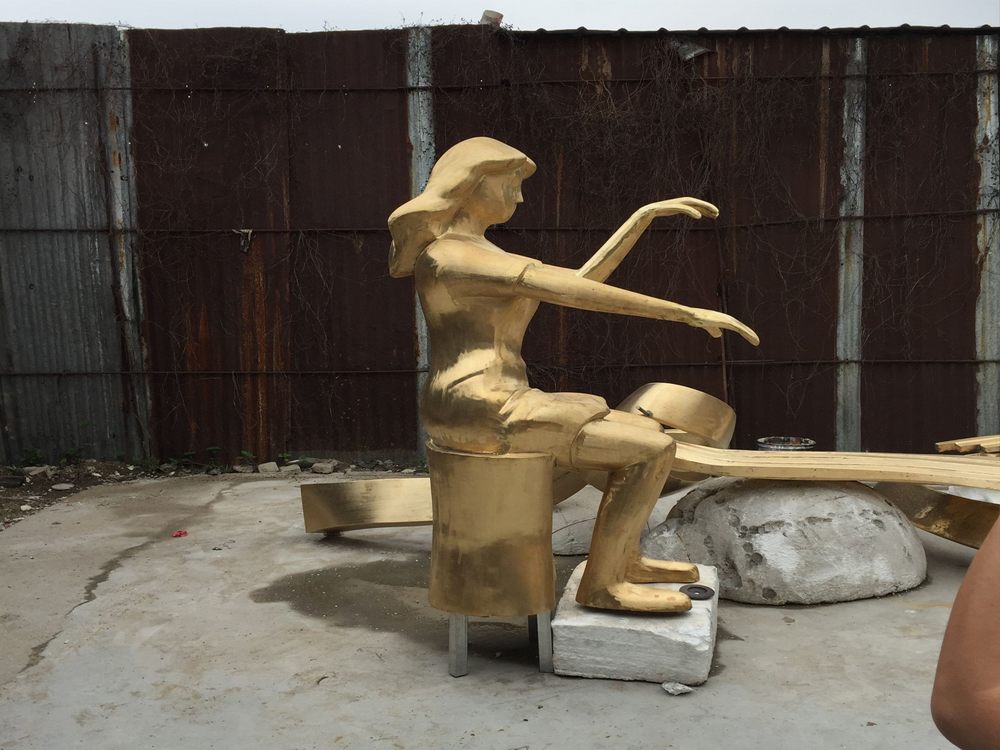
Creating flawless porcelain sculptures requires meticulous attention to glaze application and firing processes. Artists employ several strategies to prevent common defects like pinholes and crawling.
1. Proper Bisque Firing: Ensuring the bisque firing reaches the correct temperature (typically 1650°F–1940°F) removes organic residues and moisture, reducing pinhole risks.
2. Glaze Consistency: Artists adjust glaze viscosity—neither too thick nor too thin—to prevent crawling (uneven shrinkage). A well-mixed glaze with balanced water content adheres smoothly.
3. Layering Techniques: Applying multiple thin layers instead of one thick coat minimizes pinholes caused by trapped air or gases during firing.
4. Controlled Drying: Slow, even drying of glazed pieces avoids rapid shrinkage, a key cause of crawling. Some artists use humidity-controlled environments.
5. Firing Schedule: A slower ramp-up during kiln firing (especially between 212°F–572°F) allows gases to escape gradually, preventing pinholes. Soaking at peak temperature ensures glaze maturity.
6. Material Quality: High-quality, finely ground materials reduce impurities that could lead to defects. Artists often test glazes on small tiles before full application.
By mastering these techniques, ceramic artists achieve durable, visually perfect porcelain finishes, turning potential flaws into artistic triumphs.