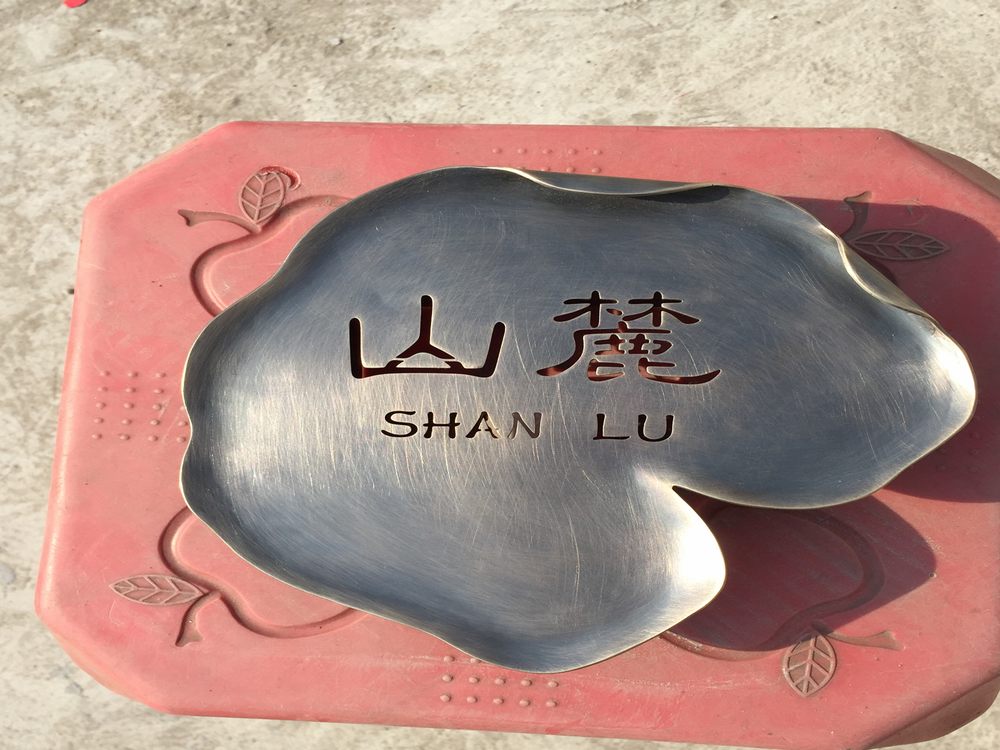
Creating porcelain sculptures for extreme climates presents unique challenges for artists, who must balance aesthetic beauty with structural durability. Porcelain, while prized for its delicate appearance, is inherently fragile and susceptible to cracking under rapid temperature changes. To address this, artists employ several innovative strategies.
First, material selection is critical. Many opt for high-fired porcelain or hybrid ceramic blends that offer greater thermal stability. These materials undergo rigorous testing to withstand freeze-thaw cycles in cold climates or intense heat in arid regions.
Second, specialized glazes play a pivotal role. Artists use engineered coatings with low thermal expansion coefficients to prevent surface cracks. Some even incorporate nano-ceramic particles for added resilience without compromising translucency.
Structural design also adapts to environmental demands. Hollow forms with reinforced internal supports distribute stress more evenly, while strategic thickness variations prevent weak points. In snowy regions, artists may incorporate sloped surfaces to shed ice accumulation.
Firing techniques are equally important. Slow, controlled kiln cycles help align clay particles for maximum strength, and post-firing treatments like thermal tempering can further enhance durability.
Installation considerations complete the process. Artists often collaborate with engineers to design custom mounting systems that allow for material expansion and contraction. In coastal areas, corrosion-resistant bases combat salt spray damage.
By merging traditional craftsmanship with modern material science, today's ceramic artists ensure their porcelain sculptures endure nature's harshest conditions while maintaining their artistic integrity. This intersection of art and engineering continues to push the boundaries of what's possible in ceramic art for extreme environments.