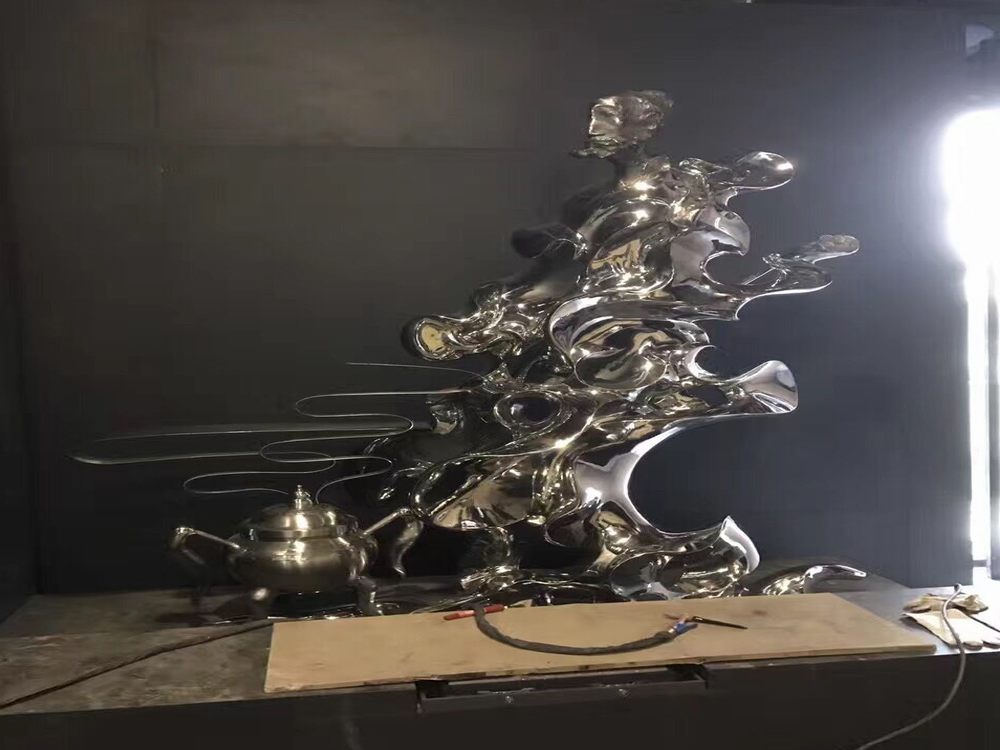
The ethereal beauty of translucent porcelain sculptures stems from meticulous craftsmanship and scientific precision. Artists begin by selecting high-quality kaolin clay with exceptional purity, as impurities can disrupt light transmission. The clay body is painstakingly worked to achieve uniform thinness - often just 1-2mm - while maintaining structural integrity.
Specialized glazing techniques enhance the light-permeable quality. Many artists use crystalline glazes containing lithium or magnesium, which form microscopic glass structures during firing. The firing process itself is critical, with precise temperature control between 1200-1400°C allowing partial vitrification without complete opacity.
Some contemporary artists incorporate innovative methods like:
1. Layering different clay densities to create gradient transparency
2. Embedding optical fibers in the clay matrix
3. Using computer-modeled perforation patterns
The translucency effect ultimately depends on three factors: material purity, wall thinness, and controlled light refraction through the ceramic microstructure. Master porcelain artists often spend years perfecting their unique translucent formulas, guarding these techniques as closely held trade secrets.