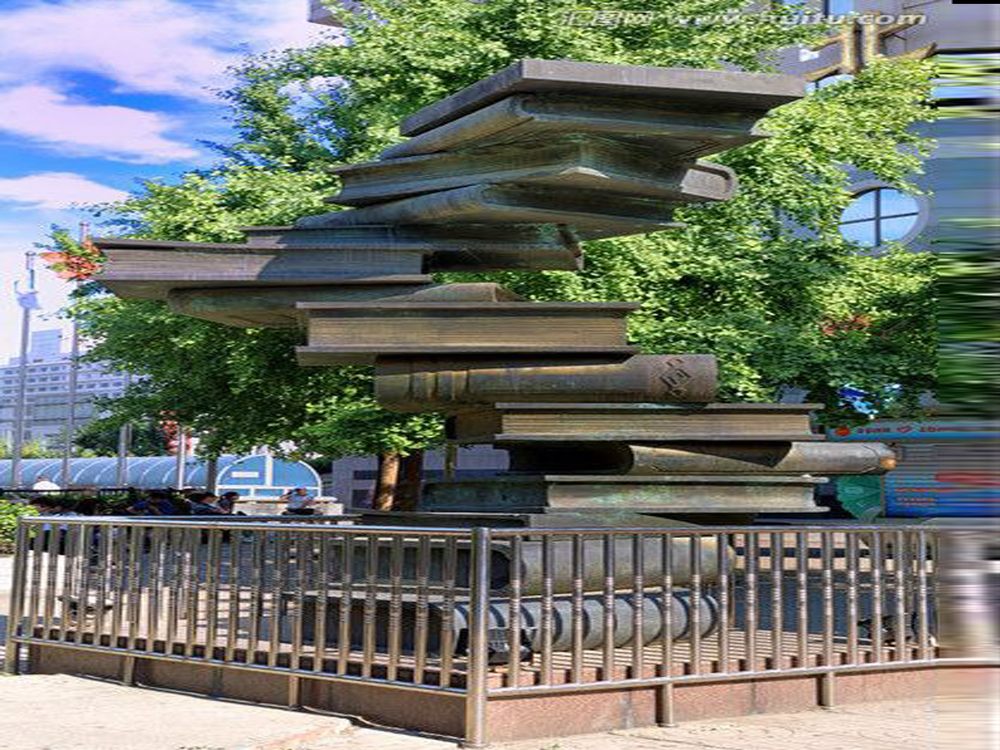
Porcelain sculptures, long admired for their elegance and durability, are increasingly adapting to sustainable and zero-waste production principles. Artists and manufacturers are embracing innovative methods to minimize environmental impact while maintaining artistic integrity.
One key approach involves material optimization. By using precise 3D modeling and advanced molding techniques, creators reduce excess clay waste during shaping. Leftover clay and trimmings are collected, rehydrated, and reused in new projects, closing the material loop.
Glazing processes have also evolved. Traditional lead-based glazes are being replaced with non-toxic, mineral-based alternatives. Water-based application methods reduce chemical runoff, while excess glaze is filtered and recycled. Some studios even employ solar-powered kilns to cut fossil fuel dependence.
The circular economy plays a vital role. Broken or unsold pieces are crushed into grog (granulated porcelain) and incorporated into new clay bodies, giving them unique texture while preventing landfill waste. Artists are also designing modular sculptures that can be repaired or repurposed rather than discarded.
Packaging innovations include biodegradable cushioning materials and minimalist designs that use 100% recycled paper. Some studios partner with local businesses to source discarded materials like wood ash for glaze experiments.
Through these methods, porcelain sculpture production is transforming into a model of sustainable craftsmanship, proving that fine art can harmonize with environmental responsibility. The industry's shift demonstrates how traditional mediums can evolve to meet modern ecological challenges without sacrificing quality or aesthetic value.