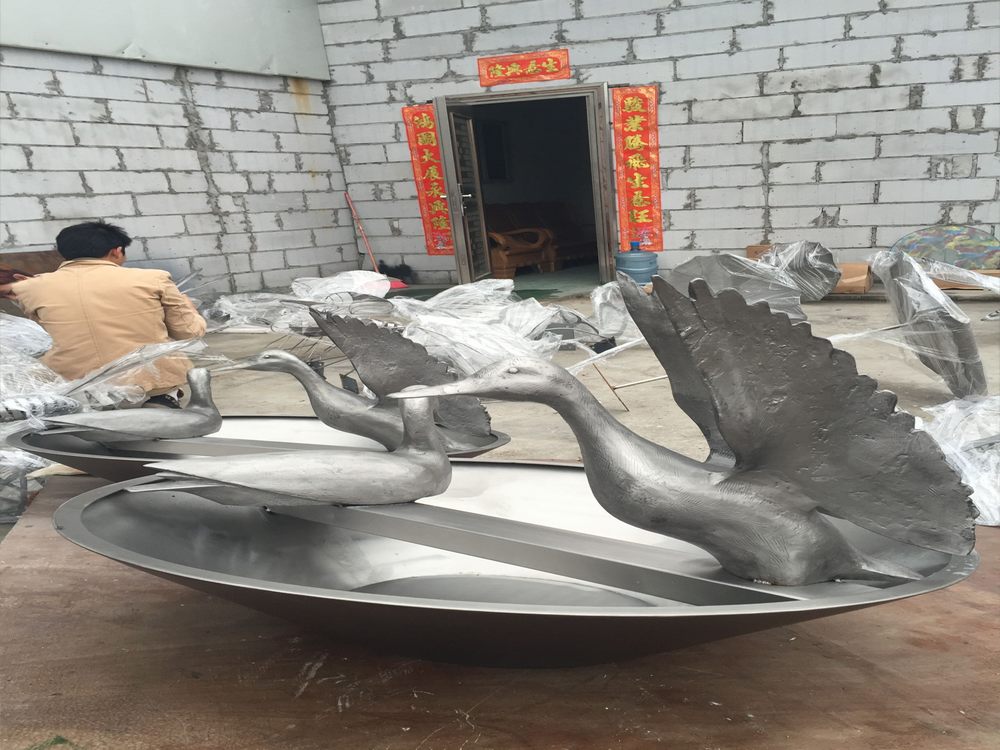
The production of porcelain sculptures is a meticulous art form that demands precision and expertise at every stage. Among the most critical phases are clay preparation, shaping, drying, bisque firing, glazing, and final firing.
1. Clay Preparation: The foundation of any porcelain sculpture begins with selecting high-quality kaolin clay. It is purified, kneaded, and aged to achieve the right consistency, ensuring flexibility and strength.
2. Shaping: Artists use hand-molding, wheel-throwing, or slip-casting techniques to form the sculpture. This stage requires exceptional skill to capture intricate details and maintain structural integrity.
3. Drying: The shaped piece is slowly air-dried to remove moisture. Uneven drying can lead to cracks, making controlled humidity essential.
4. Bisque Firing: The dried sculpture undergoes its first firing at around 900–1000°C. This step hardens the clay, making it porous enough to absorb glaze.
5. Glazing: A carefully formulated glaze is applied to enhance aesthetics and durability. The glaze composition affects the final color and texture.
6. Final Firing: The glazed piece is fired at 1200–1400°C, vitrifying the clay and glaze into a luminous, durable finish. Temperature control is crucial to avoid defects.
Each stage is interdependent, and mastering them ensures the creation of exquisite, long-lasting porcelain sculptures.