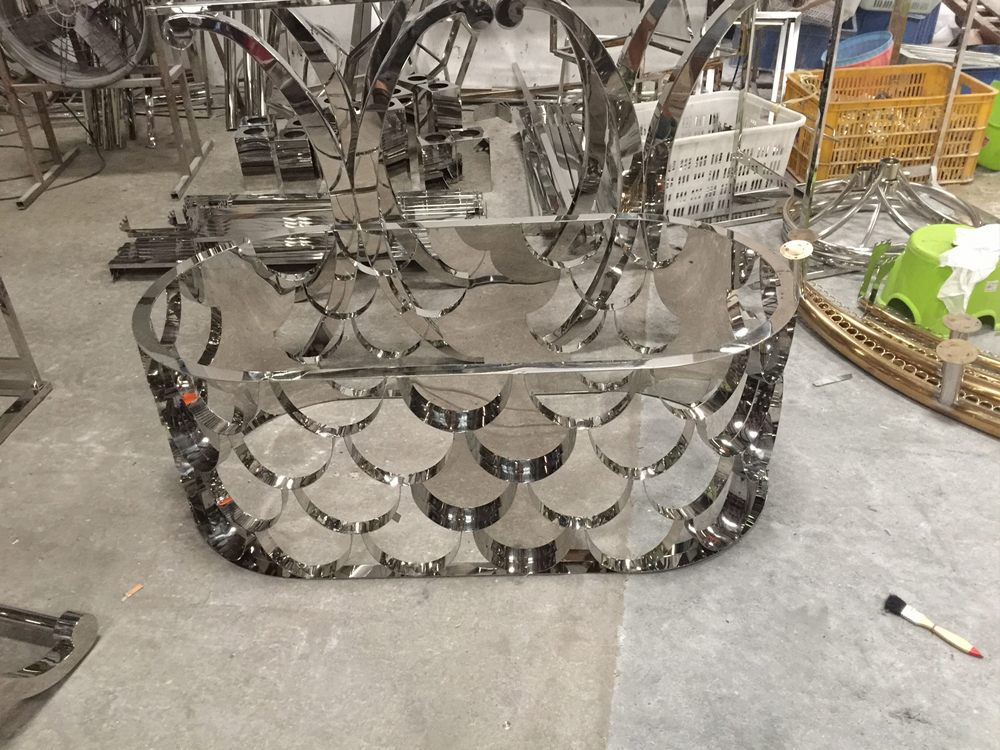
Scaling up the production of porcelain sculptures without compromising quality presents a unique set of challenges that blend artisanal craftsmanship with industrial precision. The delicate nature of porcelain demands meticulous attention at every stage, making mass production particularly complex.
Material consistency emerges as a primary hurdle. Porcelain's composition requires exact clay mixtures and mineral ratios, which become harder to maintain across larger batches. Even slight variations can affect the final product's strength, translucency, and firing behavior.
Skilled labor shortages compound these difficulties. The creation of high-quality porcelain sculptures demands years of specialized training in molding, glazing, and firing techniques. Rapid expansion often leads to diluted expertise as new artisans require extensive training periods.
Firing process control becomes exponentially more challenging at scale. Kiln temperature variations, even by a few degrees, can ruin entire batches. Larger production volumes require multiple kilns operating in perfect synchronization - a feat that tests even experienced manufacturers.
Quality assurance grows more complex with increased output. Each piece requires individual inspection for hairline cracks, glaze imperfections, and structural integrity. Automated systems struggle with porcelain's nuanced quality markers that human experts traditionally assess.
Supply chain management for specialized materials adds another layer of complexity. High-grade kaolin, feldspar, and other raw materials must meet exacting standards, with reliable suppliers becoming crucial as demand grows.
Successful scaling requires balancing traditional techniques with modern innovations. Some manufacturers implement hybrid approaches, maintaining handcrafted elements for critical details while incorporating precision molds for repetitive components. Others develop rigorous training programs to preserve quality standards while expanding their workforce.
The solution lies not in choosing between scale and quality, but in reimagining production processes to accommodate both. This often involves significant investment in technology, training, and quality control systems - proving that porcelain's enduring beauty comes at a price of constant innovation.