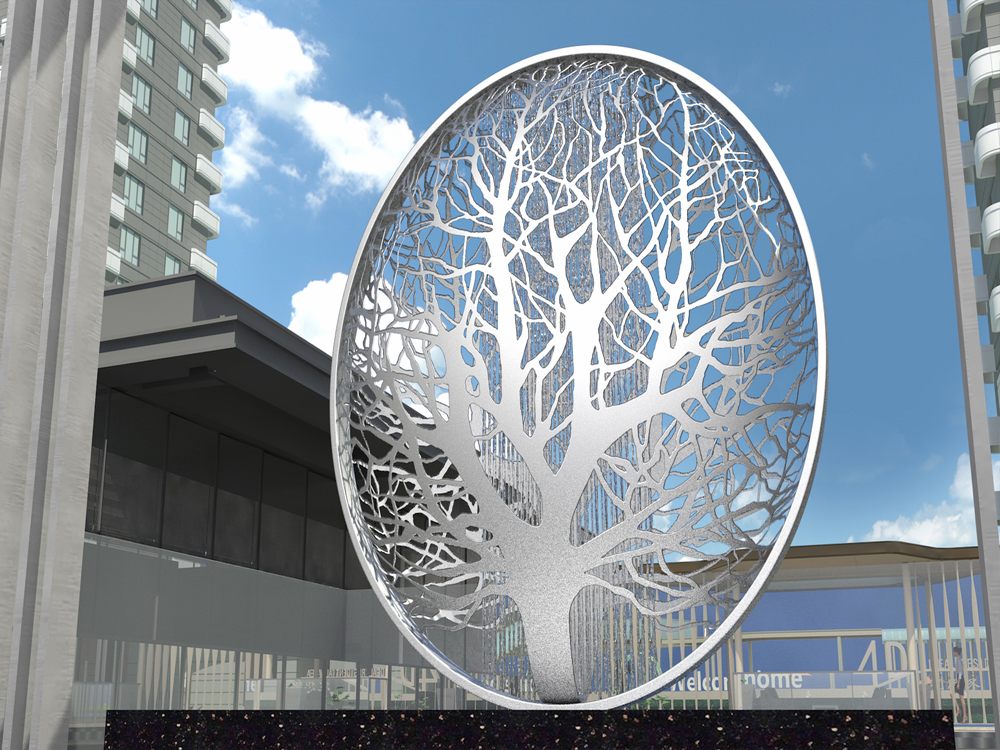
Firing large porcelain sculptures requires a kiln that meets specific technical and practical demands. Here are the key factors to consider when selecting the right kiln:
1. Size and Capacity: Ensure the kiln’s interior dimensions accommodate your sculpture’s height, width, and depth. A spacious chamber prevents uneven heating and allows proper airflow.
2. Temperature Control: Precision is critical for porcelain. Look for kilns with advanced digital controllers to maintain consistent temperatures, especially for high-fire porcelain (up to 1300°C or higher).
3. Heating Uniformity: Opt for a kiln with multiple heating elements or a downdraft design to distribute heat evenly, reducing the risk of cracks or warping in large pieces.
4. Durability and Insulation: High-quality refractory materials, such as ceramic fiber or brick linings, improve energy efficiency and longevity, essential for frequent high-temperature firings.
5. Ventilation and Safety: Proper venting systems are vital to release fumes and prevent glaze contamination. Consider downdraft or external venting options for larger kilns.
6. Energy Efficiency: Electric kilns are common for porcelain, but gas kilns may suit larger projects. Compare power consumption and fuel costs to balance performance and budget.
7. Ease of Loading: Front-loading or top-loading designs should align with your workspace and sculpture size. Some kilns offer removable shelves or doors for easier access.
By evaluating these factors, artists and studios can invest in a kiln that ensures flawless results for their large porcelain creations.