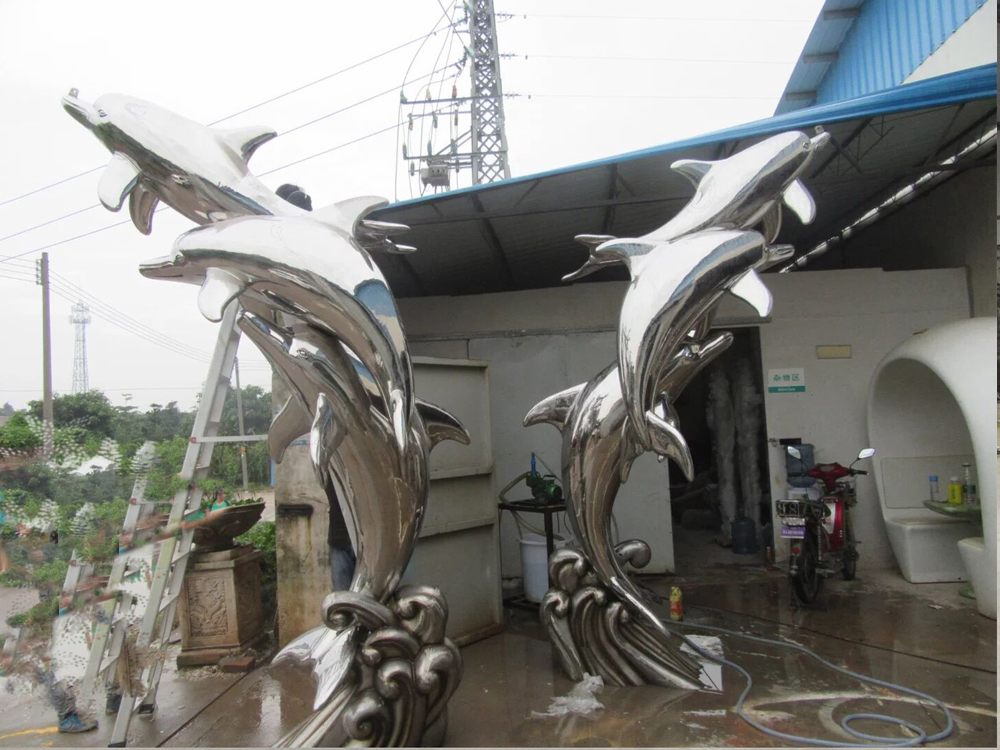
Creating porcelain sculptures with hollow interiors presents a unique set of challenges that test the limits of ceramic artistry. One of the foremost difficulties is maintaining structural integrity. The delicate nature of porcelain, combined with the thin walls required for hollow designs, increases the risk of cracking or collapsing during shaping and drying.
Another critical challenge is achieving uniform wall thickness. Uneven sections can lead to stress points, causing the piece to warp or break in the kiln. Artists must master precise hand-building or wheel-throwing techniques to ensure consistency.
The drying process also demands careful attention. Hollow sculptures dry unevenly, with exterior surfaces hardening faster than interior ones. This imbalance can create internal stresses that result in cracks. Slow, controlled drying in a humidity-controlled environment is essential.
Kiln firing introduces further complications. The high temperatures required to vitrify porcelain can cause trapped air inside hollow sections to expand, potentially exploding the piece. Ventilation holes or strategic design modifications are often necessary to prevent this.
Lastly, the fragility of hollow porcelain sculptures makes them vulnerable to damage during handling and transportation. Artists must consider durability from the initial design phase, often reinforcing stress points or creating protective packaging solutions.
Mastering these challenges requires patience, skill, and an intimate understanding of porcelain's behavior at every stage of creation. The reward is breathtaking sculptures that showcase both artistic vision and technical prowess.