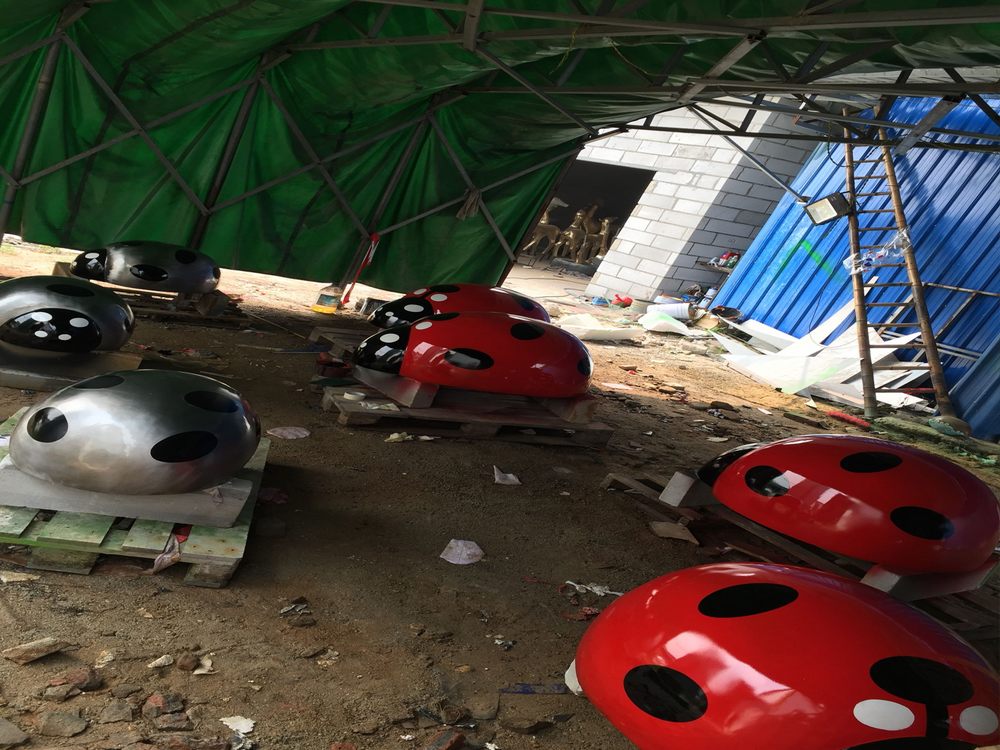
Ceramic artists face a significant challenge when working with clay: shrinkage during drying and firing. As moisture evaporates and clay particles bond under heat, the material contracts, often leading to cracks or warping. To address this, skilled artisans employ a variety of techniques.
During the drying phase, artists control the environment to ensure even moisture loss. Slow drying under plastic sheeting or in humidity-controlled spaces prevents rapid contraction. Some use grog (pre-fired clay particles) or sand to reduce overall shrinkage by providing structural support.
The firing process demands even greater precision. Artists carefully select clay bodies with known shrinkage rates, often testing samples before committing to large pieces. Kiln programming plays a crucial role - gradual temperature increases allow uniform particle bonding, while sudden changes can cause catastrophic failure.
Advanced solutions include using paper clay (which incorporates cellulose fibers to minimize cracking) or creating intentional seams in larger works to accommodate movement. Many contemporary ceramicists document shrinkage percentages for different clay bodies and firing temperatures, creating personalized guides for consistent results.
Through these methods, artists transform what could be a limitation into an understood and managed aspect of their creative process, ensuring their ceramic works emerge from the kiln as envisioned.